The Sustainability of Automated Parking with EV Charging
Required Equipment
A common question about automated parking revolves around what equipment and elements are required for the system. Let us first consider the requirements of conventional parking garages. They may seem simple, but there are actually numerous elements. There is the concrete deck, of course, and lines painted to delineate each space. But so much more is required: tall ceilings to accommodate the human stature, wide lanes for drivers to safely traverse the garage, wide spaces to accommodate opening of doors, bumpers to delineate where to stop, wide ramps for drivers to get from floor to floor, lighting for safety and security, exhaust systems, elevators, stairways, and so on.
An automated system does not require these elements, but it does have a different set of requirements. An APS generally requires, at the minimum:
- A support structure for the vehicles and equipment within the APS;
- A transfer area;
- A turntable;
- A vehicle lift;
- A transfer car (t-car) with satellite;
- software controls; and
- An electric vehicle (EV) charging system.
We will now consider each of these requirements separately.
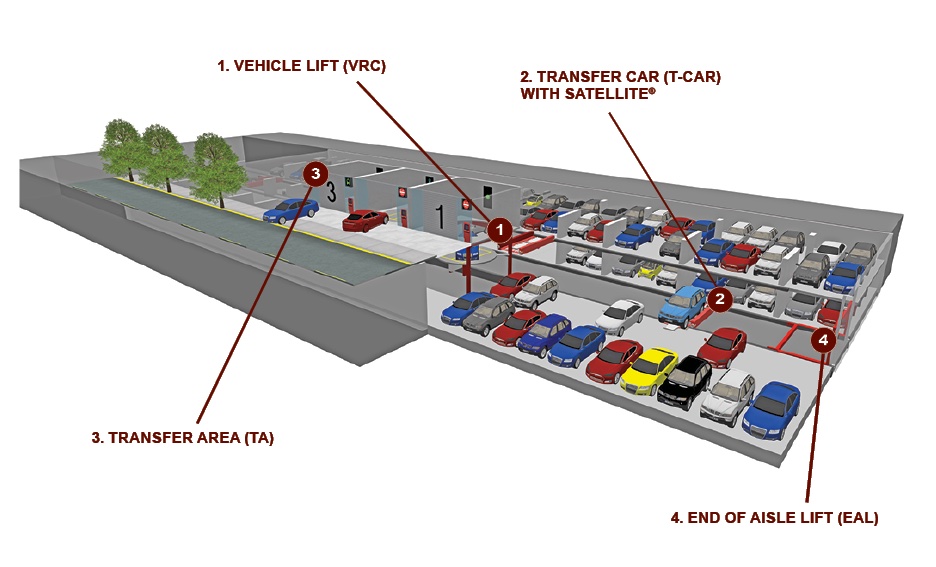
Support Structure for Vehicles and Equipment
The support structure can be a concrete slab, a steel frame with a steel or composite deck, or a hybrid structure. The choice of structure type is project specific and dependent upon such factors as its location, other structural loads in the proximity of the APS, client preference, and code requirements.
Transfer Area
While not technically a piece of equipment, the transfer area is a necessary element of the system. Transfer areas are roughly the size of a single-car garage and designed to be aesthetically pleasing to ensure each user feels safe and welcome. The transfer area is equipped with sensors to ensure that the vehicles do not exceed the allowable dimensions or weight that can be safely stored, motion sensors providing additional safety for the users, a display screen to instruct the users where to position their vehicles and other pertinent information, and automated doors to allow vehicles to enter and leave the transfer area.
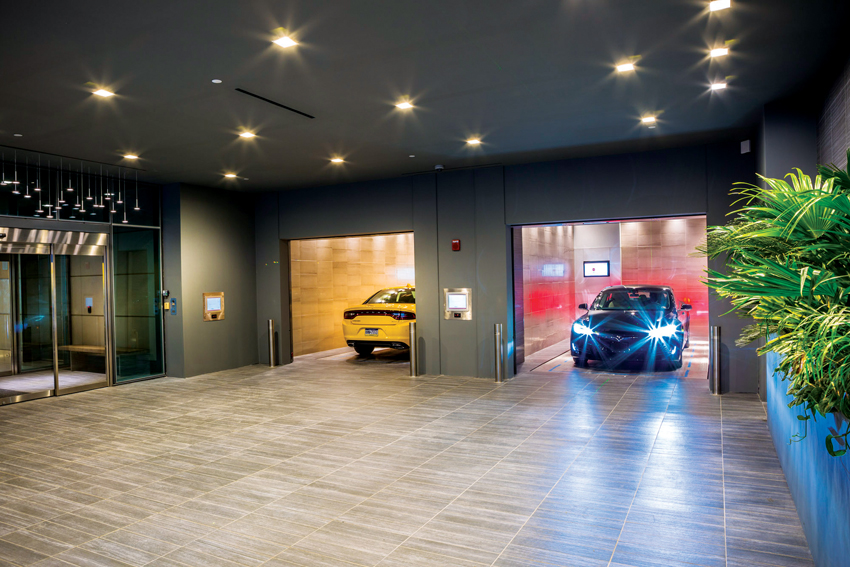
Because the transfer area is the only part of the system that users experience, creating a luxury, stylish transfer environment makes sense.
Turntable
Turntables rotate vehicles within the APS so that they are facing in an outward direction when leaving the APS. Turntables are generally located within the transfer areas but can also be in other areas of an APS.
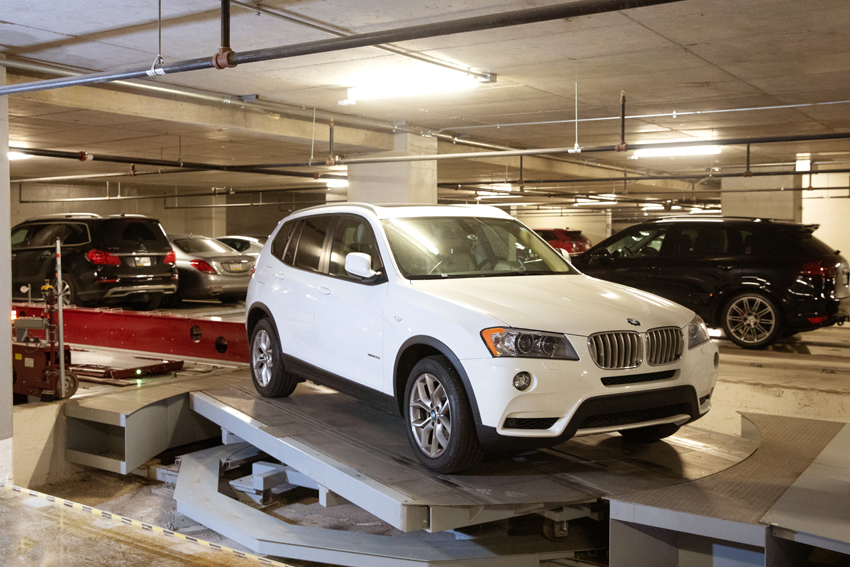
A turntable rotates a vehicle in an APS so it is facing in an outward direction when the user arrives for retrieval.
Transfer Car with Onboard Satellite
The transfer car (t-car) provides the horizontal movements within an APS. Its onboard satellite with clasp arms collects and deposits vehicles to and from the t-car directly onto a flat surface. There is no need for a pallet or car stand in every storage location. The satellite has two parts, which can move independent of one another, providing the ability to adjust its clamp arms to accept a wide variety of vehicle wheelbases.
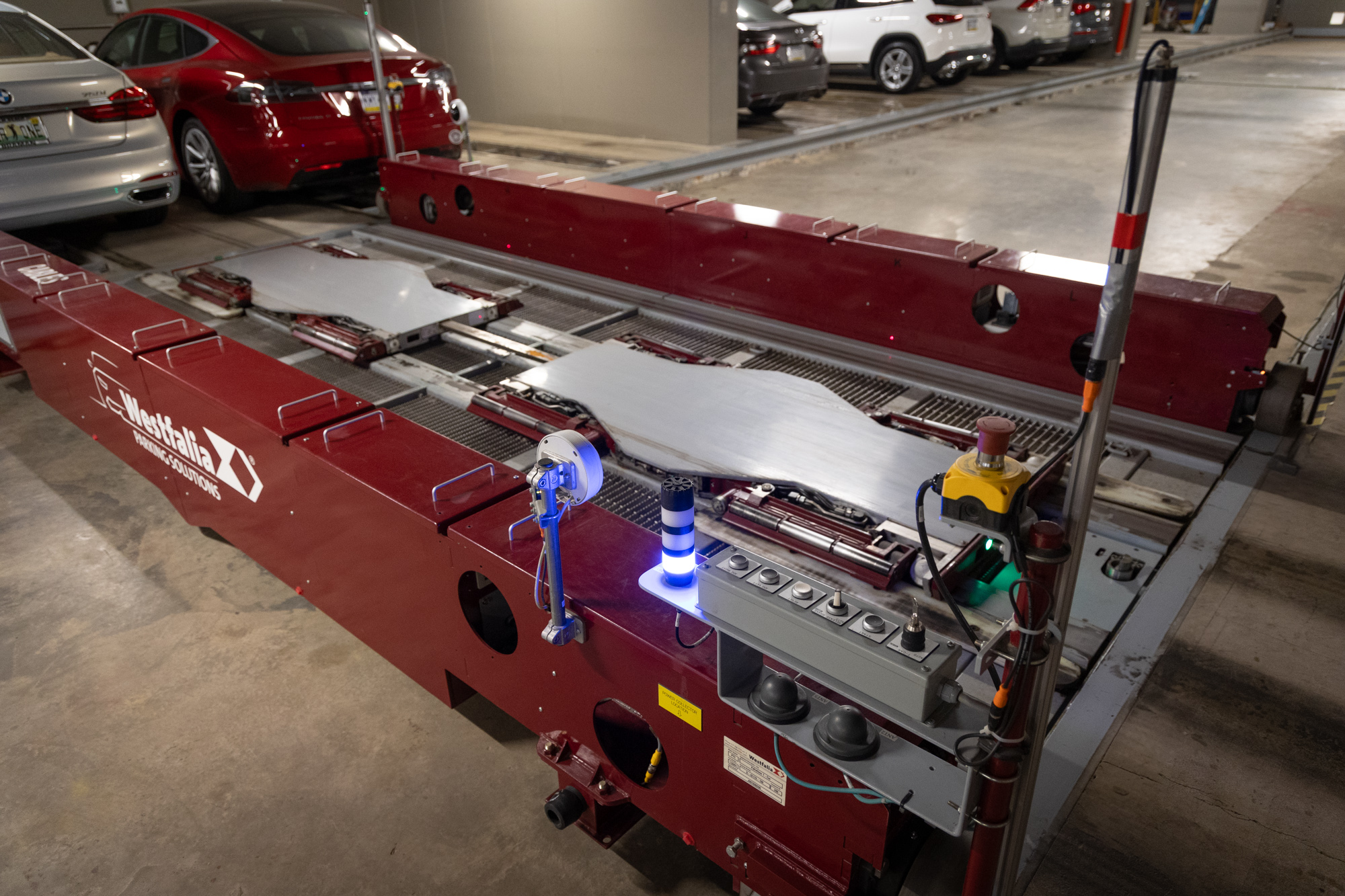
A vehicle is retrieved from its storage location and transported onto a transfer car.
Once a vehicle has been collected from a transfer area or lift, the t-car moves horizontally to position the vehicle in front of a designated storage position. Once the t-car is positioned, the vehicle is stored using the satellite, which drives into the storage lane and deposits the vehicle. There can be multiple vehicles stored in each storage lane, which can be located on both sides of the t-car aisle.
Architect Tip: Depending on the development type and throughput and redundancy requirements, a rough rule of thumb is 50 to 60 parking spaces per t-car.
Vehicle Lift
The vehicle lift(s) provides the vertical movement of all vehicles within the APS. There are two types of vehicle lift types: an end-of-aisle (EOA) lift and a side-of-aisle (SOA) lift.
EOA lifts are positioned at one or both ends of the t-car aisles and can move a t-car, with or without a vehicle, to any parking level within the APS. EOA lifts allow t-cars to move from level to level within the APS. A maximum of two EOA lifts can be used in an APS.
SOA lifts are positioned to the side of the t-car aisle and can also be located within a transfer area. SOA lifts only move vehicles between the different levels of an APS but never move t-cars.
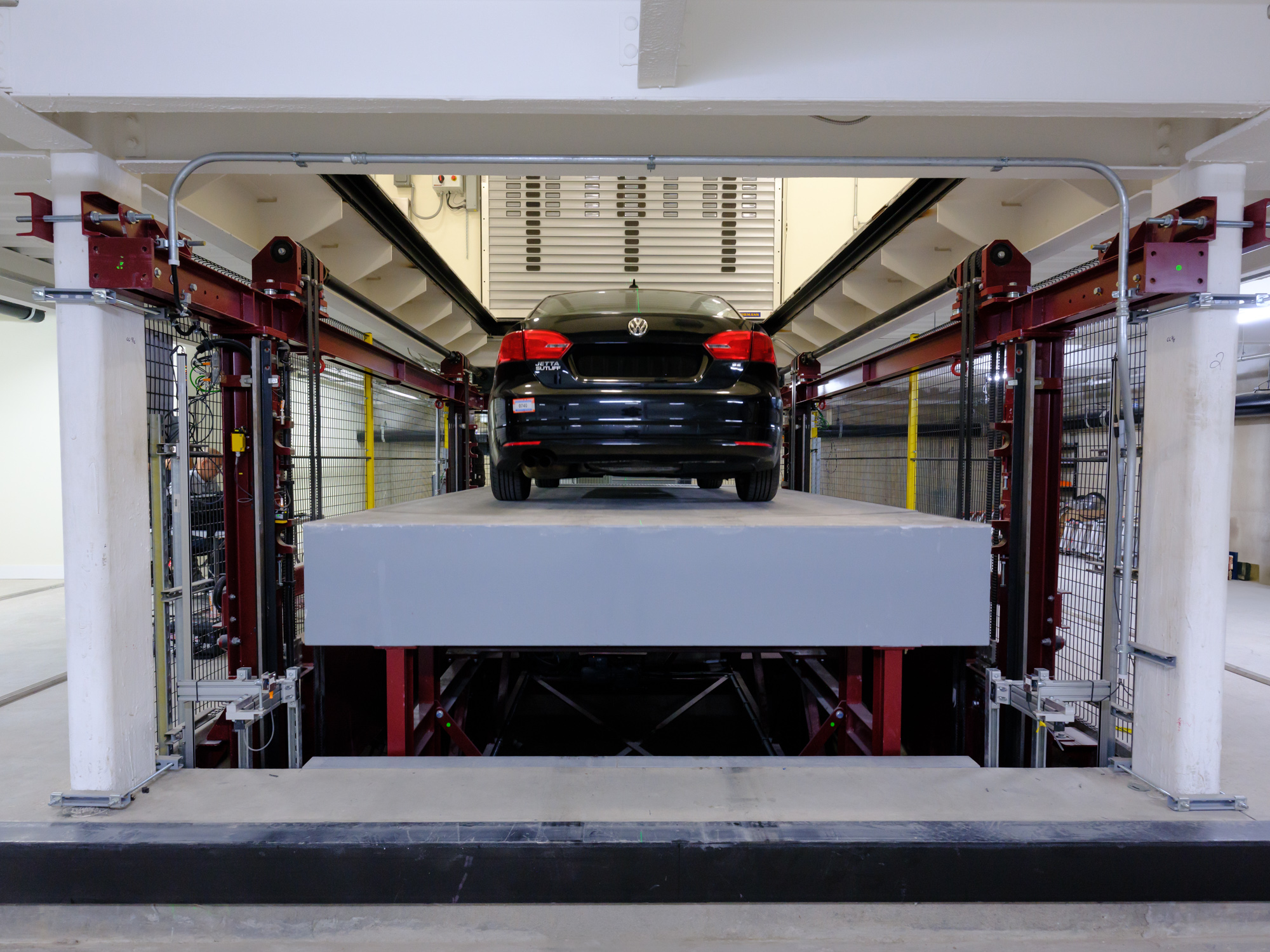
The vehicle lift moves the vehicle from the transfer area to its designated storage level.
Architect Tip: Often one EOA lift is fitted to an SOA lift APS to provide system redundancy.
SOA lift systems generally provide a higher throughput or speed than EOA lift systems, and t-cars generally operate only on designated parking levels.
Software Controls
These are comprised of:
- The programmable logic controller (PLC) or machine-control system, with associated software, that is responsible for turning on motors and receiving/interpreting signals from the sensing devices located on each piece of parking equipment.
- The parking controls system (PCS), a PC-based upper-level management software, is responsible for issuing instructions to the PLCs and other equipment and managing data, such as mission logs, occupancy levels, EV charging data, and user information. The PCS is typically stored locally on a server within the APS facility.
- The human machine interface (HMI) allows operators and maintenance technicians to interface with the machinery in automatic, semi-automatic, and manual modes and with users to confirm that their vehicles are authorized for storage within the APS. The HMI also gathers required EV charging information from users when applicable.
Watch a video of the operation here.