Net Zero Performance and Curtain-Wall Systems
Learning Objectives:
- Define fundamental terms such as net-zero energy, net-zero carbon, absolute zero carbon, and carbon neutrality, and demonstrate familiarity with applications of these concepts as defined by U.S. and international organizations.
- Recognize the range of available curtain-wall systems that contribute to a building’s performance, including widely available products, advanced or aspirational technologies, and traditional or low-technology approaches.
- Recognize several recent and contemporary construction projects that have achieved or approximated net-zero carbon metrics through high-performing curtain-wall systems and complementary approaches.
- Understand the long-range environmental effects of designing and building with the range of facade technologies, placing the contribution of curtain walls in the context of a building’s overall performance.
Credits:
As an IACET Accredited Provider, BNP Media offers IACET CEUs for its learning events that comply with the ANSI/IACET Continuing Education and Training Standard.
This course is approved as a Structured Course
This course can be self-reported to the AANB, as per their CE Guidelines
Approved for structured learning
Approved for Core Learning
This course can be self-reported to the NLAA
Course may qualify for Learning Hours with NWTAA
Course eligible for OAA Learning Hours
This course is approved as a core course
This course can be self-reported for Learning Units to the Architectural Institute of British Columbia
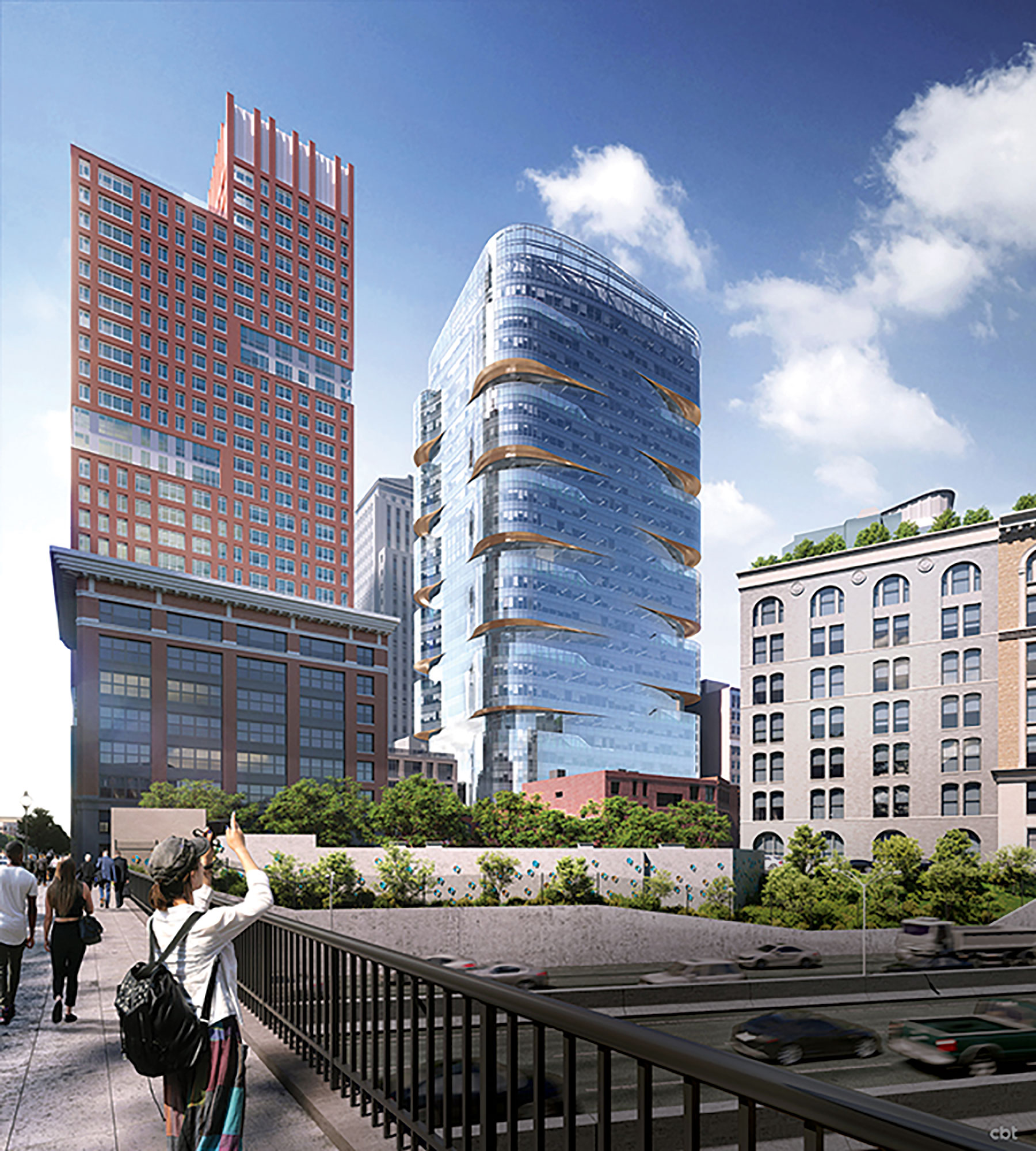
Photo courtesy of CBT Architects
In plans for 380 Stuart in Boston's Back Bay, careful product selection, creative design strategies, and a willingness to invest in triple glazing are setting new standards for the energy performance of curtain walls.
As a metric, a goal, a marketing instrument, a criterion within certification systems, or a buzz phrase, the term net zero can mean different things to different people. Like green, sustainable, or eco-friendly, net zero is sometimes used loosely to indicate good intentions without a rigorous foundation of greenhouse gas (GHG) emission measurement to support it. Nevertheless, through the efforts of conscientious designers and the forward-looking segments of the building-products industries, net zero and near-net-zero buildings have moved from an intention to a reality, and today’s architects are in a position to advance decarbonization by incorporating net zero standards into their designs. Curtain walls, as essential contributors to (or detractors from) a building’s energy performance, are one of the critical sites for these efforts.
Architects and builders may view net zero, or at least some claims about it, with a degree of justifiable skepticism and caution. Canadian Minister Catherine McKenna, the former chair of the United Nations’ High-Level Expert Group on the Net-Zero Emissions Commitments of Non-State Entities, said at the 27th Conference of the Parties (COP27, Sharm El-Sheikh, Egypt, 2022) that “the planet cannot afford delays, excuses, or more greenwashing,” crediting some organizations with making tangible, purposeful progress on emission reduction while charging that in other areas, “too many of the net zero pledges are... little more than empty slogans and hype” (COP27 “Zero Tolerance”).
The High-Level Expert Group, created by Secretary-General António Guterres after COP26 in Glasgow, 2021, identified several patterns of conduct by non-state actors (industry, financial institutions, cities, and regions) that compromise the value of the net zero and “net-zero-aligned” concepts. These categories of greenwashing include claims of net zero status by entities that continue to build or invest in new fossil-fuel supply; purchases of low-integrity credits; focusing on reducing emissions intensity rather than absolute emissions, or tackling part of emissions rather than the full value chain of Scopes 1, 2, and 3 (as defined by the GHG Protocol to address operational and embodied carbon, direct and indirect); lobbying to undermine governmental climate policies; and reliance on voluntary initiatives rather than regulated requirements for net zero (U.N. High-Level Expert Group, Integrity Matters, p. 7). The group’s report insists on “not only long-term pledges but also short-term science-based targets” and public reporting with verifiable, comparable information on these actors’ progress.
Yet regardless of misuse of the term and contention over its meaning, the net zero concept can guide and motivate efforts to improve buildings’ performance. Net zero at its best designates a serious commitment to managing both operational and embodied carbon, achieved through the deployment of a full range of systems and technologies, both familiar and new. Since facades account for a substantial proportion of a building’s energy use and consequent carbon footprint, optimizing the function of a curtain wall offers considerable leverage toward GHG emission reduction on the single-building scale and beyond. Net zero codes in some locations are driving impressive achievements despite the inherent challenges in the thermal properties of curtain-wall systems (see Case Studies, “380 Stuart Street”).
NET ZERO, ABSOLUTE ZERO CARBON, AND OTHER BENCHMARKS
Net zero can be seen not so much as an innovation by the architects and engineers of the developed world, comments Dennis Vermeulen, AIA, LEED BD+C, partner at Marvel in New York, but as a traditional global norm reflecting the frugal energy-use patterns of nonindustrial societies. “The skeptic in me sometimes thinks that it’s intentionally not clear,” he says, “so people can make more out of things.” He recalls a conversation early in his career, after he had been studying net-zero buildings and “crowing, ‘Oh, we’re going to do a net-zero building,’ and someone I was working with said, ‘You know, about half the world lives net zero right now.’ And I think in terms of how the term should be used, that’s actually the correct term. You don’t heat or cool your home. Your home is actually built out of local material. Maybe it’s bio-based material; it’s what you have. It’s certainly not much bigger than what you need. In the last, maybe, 20 years, that’s changed. So I think more and more people are living in cities and living in architectural environments, but to me, the correct concept of zero is really zero.”
In the developed world, there are more near-net-zero buildings, net-zero-ready buildings, and buildings that use offsets to reach a zero emission measurement than buildings that can satisfy rigorous net zero criteria. The net zero concept, to Vermeulen and other practitioners, is most useful when interpreted in a broad context. “Standardization of the terms would really be helpful,” he says. “When we look at it as design, we’re really looking at carbon footprint, so that’s everything from extraction of materials, fabrication of systems, shipping it to the site, installing it, and then building a building, and then operating a building. And even how you would dismantle a building and recycle those materials: that’s what we’d like to look at. And when we do that, of course, we’re very far away from the kind of zero carbon that we want to be. But every day, I think we get a little bit better.”
Shanta Tucker, PE, LEED AP BD+C, director at the New York office of environmental consultants Atelier Ten, credits the American Society of Heating, Refrigerating and Air-Conditioning Engineers (ASHRAE) with offering “a pretty good working definition that combines an energy-efficient building that has no fossil-fuel use with the ability to produce as much electricity locally as it uses within a year.” A net-zero building in this sense is metered and connected to the utility grid, has infrastructure that produces electricity (e.g., photovoltaics [PVs] where applicable), and may also have some purchased green power.
The U.S. Department of Energy (DOE) has incorporated the ASHRAE standard by reference in its newly published definition, requiring a building to be highly energy-efficient, free of on-site GHG emissions from energy use, and powered solely from clean energy. DOE’s fuller definition of those three criteria, the relevant report states, is a minimum standard, not a regulatory standard in itself but one to be used by public or private entities determining buildings’ zero-emission status:
- Highly energy-efficient: Buildings must demonstrate exceptional energy efficiency, placing them among the top performers in the market or achieving significant reductions in energy use compared to model codes.
- Free of on-site emissions from energy use: Zero-emissions buildings must eliminate direct GHG emissions from on-site energy consumption.
- Powered solely from clean energy: All energy used by the building must come from carbon-free sources, whether generated on-site or procured from off-site sources. (U.S. DOE, “National Definition of a Zero Emissions Building”)
The DOE definition also does not permit carbon offsets, an approach drawing frequent charges of allowing fudging by entities continuing to emit GHGs. DOE’s interpretation of a zero-energy building is based on source energy use intensity, one of multiple metrics used in the field (for an overview of ten common metrics provided by the Scottish firm Integrated Environmental Solutions, see Buckley).
Mic Patterson, PhD, LEED AP BD+C, ambassador of innovation and collaboration at the Facade Tectonics Institute (FTI), agrees with the UN group about undisciplined interpretations of net zero, associating it with other terms often used imprecisely (sustainability, regenerative architecture, etc.) in a category he calls “sustainababble.”
To use net zero purposefully, “the first thing we need to do is agree on a definition,” he says. “I don’t think we even understand what net zero is, and I know we don’t know how to achieve it. We went for a long time ignoring the embodied-carbon part of the carbon equation, and that is half of the equation. You’ve got operational carbon; you’ve got embodied carbon. We were, for decades, solving the operational problem by adding to the embodied carbon burden without quantifying that. We had just left that out of the equation entirely.” It is also possible, he suggests, that another unrecognized footprint component will require recognition: “It’s like layers of the onion, and one of the biggest, most recent layers was embodied carbon. Well, what are we going to find out next? There will be a next.”
Life cycle assessment (LCA), the only means of assessing embodied carbon, “remains at least as much an art form as it is a science,” Patterson adds, with different practitioners often providing different answers to the same problem. Another complication he mentions is that the primary tools for LCA, environmental product declarations (EPDs), are frequently entrusted to manufacturers, who hire LCA consultants, so that without independent verification, another abbreviation may plausibly be considered: COI, conflict of interest.
The gap between the intention to reduce emissions and reliable means of reaching net zero, Patterson observes, is not insurmountable. LCA tools and databases such as EC3 and Tally (see “A Number and a Story: Optimizing Design and Construction to Reduce Embodied Carbon”, Architectural Record, July 2024), he notes, are making it easier to assess embodied carbon during material selection; progress continues regardless of degrees of precision. “A lot of good designers and good firms are truly trying to figure this out and move in that direction.... It’s a great aspiration. We don’t have the tools that we need to ensure that we’re hitting it, and we don’t have the strategies or tools to do that. But to do everything we can with what we have is critical.”
Vermeulen’s colleague at Marvel, Jeremy Iannucci, AIA, LEED BD+C, suggests that “either net or neutral is the misleading word there, where it implies a balancing between the carbon or the energy and either offsets or further energy production. Absolute zero carbon is the actually aspirational goal, where you’re minimizing the carbon emissions throughout the entire process.” The discussion of balancing, he continues, “does make the goal accessible. A lot of developers are going to be in the position where buying offsets is still the correct and beneficial way to go. But I do think reduction should be the focus... not just balancing, not net, not neutral, just minimizing.”
Atelier Ten often promotes the concept of absolute zero carbon rather than net zero, recognizing the broad context surrounding performance metrics. As Tucker says, “We see the absolute zero carbon as what we’re working towards, as a tool to make a road map for our work in consulting and helping clients make decisions. So the ‘absolute’ part is recognizing that it isn’t just the building, but it’s how people get there. It’s what they do once they’re in the building. It’s the life cycle of all of the demands the building makes on the outside world: what gets delivered, what gets used and discarded? And that then really opens up the conversation about transit, about food waste, what to do with renovations, and how to make decisions about long-term retrofits, short-term retrofits. And we also like to be inclusive of all building systems for construction.” As clients and collaborators become more familiar with embodied carbon as well as operational, Tucker continues, the absolute-zero criterion targets not only the footprints of the structure and enclosure but “the lights, the wires, the metals: everything that goes into the building.” Retrofitting an existing building creates opportunities to upgrade facade materials and other components in a coordinated fashion (see Case Studies, “Bronx Museum South Wing”).
“The fact that there are multiple definitions of net zero” strikes Stephen E. Selkowitz, senior advisor for building science at Lawrence Berkeley National Laboratory, “as useful, because we can tease apart the details.” He recognizes a hierarchy of strategies: “There’s what you must do, what you should do, and what’s nice to do.” Every building must “meet or beat code,” using readily available and cost-effective means; a smaller subset of major organizations that can afford to invest in designers and technologies that attain net zero (the government included, he says) should do so; and on the vanguard of innovation, experiments with technologies for which markets are not ready, or may never be ready despite years of experimentation, remain worth exploring on a proof-of-concept basis, pushing the envelope of the possible.
Selkowitz alternates between recognizing achieved and achievable gains and expressing a degree of frustration that the facade technologies associated with them are not more widely implemented. “From a ‘what can be done?’ point of view,” he says, “we know we can make a facade net zero, or net-zero carbon, net-zero energy, whatever you want it to be. We know how to do it.” On the other hand, he wonders, “Why isn’t this business as usual?” Expense, complication, and inexperience with installation, he finds, account for slow adoption of high-performing products such as triple, quadruple, “thin triple” (with an interior lite only 0.5 to 1.6 mm thick, or even a lightweight suspended plastic film) and vacuum-insulated glazing (VIG). He has evaluated a range of high-performance window technologies for the California Energy Commission (Selkowitz 2024)—“more on the residential side, but it’s conceptually similar issues,” he comments – and finds that while long-heralded innovations like VIG and aerogel continue to face barriers not limited to cost and availability, thin triple windows occupy a promising sweet spot between technical performance and potential market acceptability, though nudges from the public sector may be necessary.
“If you look at 30 or 40 years, I’m quite optimistic that these changes could happen,” Selkowitz continues. “But if you want to solve the global problem of climate change, you need to do it in 10 to 20 years, not 30 to 40. And so the question is, ‘Can it be accelerated?’ The answer is, yes, with the right policy, and the policy and technology are two parts of the same thing.” He summarizes by defining himself as “an optimist about all this stuff generally, but when it comes to the marketplace, having been doing this for 40-plus years, I’m a pragmatist about what really works and what doesn’t,” he says.
“On the one hand,” Selkowitz says, “the purist in me, and the champion, says, ‘Let’s go all the way, and let’s do it right. Let’s define zero carbon in a way that includes both operational and embodied, and is on site, and is not buying rebates from someplace else.’ But there’s another part of me that goes back to the old saying that the perfect is the enemy of the good. In the end, what you want is to reduce total carbon; if you can get a million buildings to get halfway there versus one building to go all the way there, I argue for the million buildings.”
GETTING SKIN IN THE GAME
“The industry doesn’t seem to get that the way to net zero is right through the building skin,” Patterson says. “It’s not about the facade system being secondary and focusing on the mechanical system. You’ve got to integrate the whole building performance, and the big integrator is the facade system.” An often-overlooked point about energy-conserving facades, he finds, is that despite disparate metrics and goals, “we know a lot. Not only is there a lot of knowledge, there are even a lot of products out there to deal with these things, and they’re sitting on the shelf and not being used,” even though better-performing products often have only incrementally higher costs, or even no additional cost. Developers’ tendency to consider first cost rather than life-cycle costs, he says, is a recurrent barrier to adoption of high-performance technologies such as lightweight triple glazing, transparent PVs, nonconductive integrated-glass-unit (IGU) spacers, or polymer thermal breaks.
Codes, Patterson finds, can drive improvements, but only so far, given many developers’ view of them. “The minimum performance standards are what is represented in the building codes. It’s the way that you can legally build the worst-performing building.” Owner-developers and occupant-developers such as corporate headquarters or the General Services Administration (GSA) create “opportunities to go beyond code,” he observes, “but a lot of the building that’s gone on has been spec development by [non-occupant] developers, and you can get them to move a little beyond code so that they can raise a flag and say it’s green, or it’s got LEED credentials.”
With too little attention paid to the service life of products or buildings, Patterson continues, “We’re still selling facade systems as zero-maintenance systems” rather than planning for a level of maintenance and durability that can strengthen claims about embodied-carbon reduction. “We’re basically saying ‘You can’t maintain this; it’s good for as long as it’s good, and then you’ve got to tear it down and put a new one up.” With this short-term approach prevalent, despite the availability of durable materials and technologies, he concludes, “We have been very busy building tomorrow’s problems today.”
A facade’s contribution to a building’s energy management varies widely with its scale and form, Tucker says: slim residential buildings with a high proportion of facade area to floorplate are at the higher end of the spectrum of contribution to energy losses, while fatter buildings with large floorplates generate substantial heat on the interior while losing relatively less energy through their skin. Local climate extremes also correlate with the facade’s proportionate role: “In general, in areas that have a tighter temperature range,” she says, “your facade is going to most likely matter less, as you can design it to deal with a smaller range of conditions and be more optimized.” The facade’s contribution “could be as small as 5 to 10 percent of the energy use [or] as big as a quarter.”
From the energy modeling that Vermeulen and colleagues have performed on their projects, his estimate of curtain walls’ contribution to the emissions footprint ranges higher and implies they are a key priority. “If we’re talking about a true curtain wall, where the majority of your building is covered by a single system, that could be 80 or 90 percent of your building envelope. It’s not your roof [or other components], but it’s everything else, in which case that could have a 30 to 50 percent effect on your overall energy use in terms of heating and cooling. Even if you’re doing daylighting controls, you can actually reduce your lighting loads by using the window.”
On the embodied-carbon front over the full life cycle, Vermeulen estimates, a curtain wall may account for 5 to 7 percent of a project’s construction material, “but the materials in it are actually very carbon-intensive. Glass and aluminum are very intensive to produce, and even though we like to specify recycled aluminum, it’s actually hard to get recycled aluminum in curtain-wall profiles. There’s always a lead-time issue, and often you’re just buying it too late in the process to guarantee that you’re going to get that. So even if it’s a small percentage of your construction, it can be a pretty high part of your carbon footprint to begin with.” (Steel, he adds, being mostly recycled and more readily available, has lower carbon intensity per pound than aluminum or glass.)
The window-to-wall ratio is another key determinant of facade performance. “In New York right now,” Vermeulen says, “to meet code, you have to provide quite a bit of opaque area. So you’re either building interior walls behind the curtain wall and using spandrel glass, or you’re trying to get your curtain-wall manufacturer to give you higher-performing opaque sections, using back pans and insulation within.” A spandrel at floor plates reduces vision glass while improving envelope performance. “We look at adding insulation, particularly to opaque walls,” he continues, “and once you get to R 30, our energy models don’t show much appreciable change if you go to R 60. If you add another three, four, five inches of insulation, it really doesn’t change the energy model at that point. With glass and curtain-wall systems, you’re never going to get much more than R 4 or R 5 for the vision areas.”
In curtain walls as traditionally understood, Vermeulen says—“aluminum profiles capturing glass, clipped onto a building”—the glazing generally outperforms the profiles. “Even just double-insulated glass performs much better, just as an assembly on its own, than the aluminum framework does. So we think ‘slender profiles, big pieces of glass.’ The bigger the glass and the less aluminum you see, the better.” These systems with typical R ratings of 4 or 5, he says, are acceptable under New York City code only when manufacturers provide lab tests indicating better performance, “so we end up jumping through a lot of hoops to make buildings pass energy code.” Adding insulated walls is more complicated than popping in premanufactured panels, involving multiple trades, and “adding insulation inboard that’s not engineered in a system tends to move the dew point around, which can cause problems with condensation....We would love to see curtain-wall manufacturers look at more ways to engineer integral, opaque portions of their system” to attain higher R values. “The rule of thumb now is that you want your vision glazing in a building to be something like 40 percent of your facade, and you see curtain walls, particularly in commercial buildings, that are basically 90 percent vision glass. And we see products like that get permitted. I’m not quite sure how they do that with the code, because you just can’t get that kind of performance, even with triple glazing.”
One pathway to better insulation performance is use of alternative materials, which may involve tradeoffs between operational and embodied carbon. A Marvel project designed with net zero in mind, the One Java complex on the waterfront of Greenpoint, Brooklyn, uses a precast concrete curtain wall wrapping two towers (see Case Studies, “One Java”), though Vermeulen and colleagues recognize that precast “is not a very good material for embodied carbon.” The panels also require “somebody to go outboard and put a bead of sealant between them; there’s not a good gasketing and integral drainage system in it. So curtain wall is a great starting point, but it could do much more.” The firm has also experimented with terra cotta, a lighter, lower-carbon-intensity material, as a curtain-wall insert, deciding on that project (Brooklyn’s Bedford Union Armory) to use a metal panel system.
The need for better envelope performance is measurable both in carbon emissions and in financial terms, notes Peter Arbour, RA, Assoc. AIA, former principal at Socotec’s Vidaris and now founder of Arbour Group, a facade casting firm. “We’re familiar with the statistics,” he says: “40 percent of global carbon emissions come from buildings; in large cities like New York, the share increases to 70 percent.... The United States loses $30 billion a year in heating and cooling energy lost through the building envelope due to poor insulation. This is energy-ratepayer money that literally goes out the window.” In addition, he notes, the periodic failure and replacement of structurally glazed aluminum facades—“glass that’s warrantied for 10 years and will fail within 25 years, structurally glued onto the outside of the building facade framing”—predictably disrupts building operations and urban life. There is a pressing need, he and others contend, for facade systems that perform better in emissions metrics (ideally net zero or close) and have a substantially longer service life.
A promising newcomer among materials is Arbour’s Liquid Wall (see Figure 1), highlighted in a Curtain Wall Innovation competition and exhibition at the New York AIA chapter’s Center for Architecture in 2010-2011 and more recently awarded a grant for manufacturing support by the New York State tech incubator FuzeHub. Liquid Wall replaces aluminum in curtain-wall systems with a composite material, ultra-high-performance concrete (UHPC), in precast form with noncorrosive fiberglass polymer and steel-fiber reinforcement to constrain crack propagation under load. Liquid Wall units set replaceable double-glazed panels into the UHPC frame, which is cast with digitally manufactured formwork of polyurethane or silicone; the unit is 100 percent thermally broken, with nonconductive connectors and a polymer thermal break separating the exterior and interior. The material’s plasticity is conducive to design precision and fine tolerances: “My material supplier at the moment cast a vinyl negative of a record in UHPC, a record that he could play on a record player,” Arbour reports. “It didn’t sound great, but it would play. That’s the level of finesse in terms of achieving ornamental detailing.” “UHPC is not the concrete that we see all around us,” Arbour points out; “UHPC in the Liquid Wall uses 85 percent less cement than concrete, far less than any green concrete in the market, [and] produces 75 percent less embodied carbon than aluminum facades, because it eliminates the strip mining, smelting, and global transport associated with aluminum production.” Different UHPC products use fiberglass, polypropylene, or steel fibers for reinforcement. “The secret to UHPC is the size of the aggregate,” so where you would have sand or stone or something else, which is bonded by the cement, in this case you have aggregate components that are smaller than the cement particles. So it’s usually a quartz flour and silica fume that are powders that have a particle-packing density that makes the material impervious to anything....The limits of water and chloride infiltration into the material are fractions of a millimeter versus standard concretes, where you get up to 5 mm per year.”