Picking the Proper Mortar for Adhered Veneers
Learning Objectives:
- Identify the different types of mortars used for adhered veneers in contrast with those used for structural mortars.
- Investigate the national standards used for installations that protect the health, safety, and welfare of building occupants.
- Assess the differences between site- mixed mortar products and factory- preblended mortar products that ensure quality and safety.
- Specify adhered veneer mortar products in a variety of green and conventional buildings and formulate appropriate selections related to specific applications.
Credits:
This course is approved as a Structured Course
This course can be self-reported to the AANB, as per their CE Guidelines
Approved for structured learning
Approved for Core Learning
This course can be self-reported to the NLAA
Course may qualify for Learning Hours with NWTAA
Course eligible for OAA Learning Hours
This course is approved as a core course
This course can be self-reported for Learning Units to the Architectural Institute of British Columbia
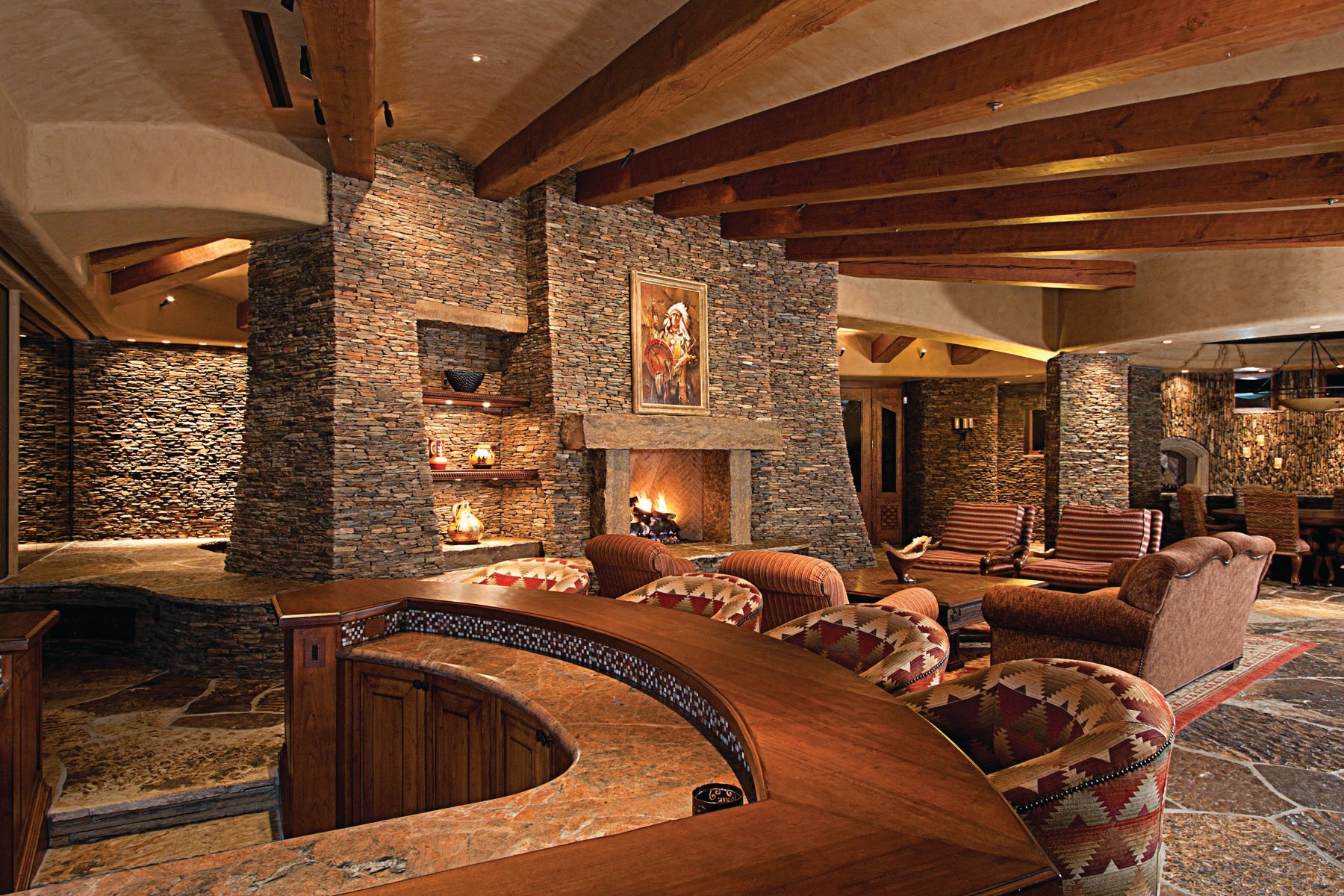
Photo courtesy of SPEC MIX
The use of the correct mortar for adhered veneers such as manufactured stone, thin natural stone, thin brick, or tile means that both interior and exterior designs will perform as intended.
It has become increasingly common for buildings to be constructed with lighter-weight materials, particularly on building exteriors. That means there has been a transition from heavier structural stone and masonry to lighter-weight structural systems using steel, reinforced concrete, or structural timber. There is still often a desire, however, for the look and durability of masonry. Accordingly, it is now more common that a thinner, lighter veneer of natural stone, manufactured stone veneers, or thin clay brick adhere to a substrate secured to the structure. In so doing, it becomes quite important that the correct mortar materials are used to adhere that veneer so it will remain in place over the life of the building without the threat of harm to people or requiring undue maintenance. This course takes a closer look at the choices for selecting and designing with adhered veneer mortars to achieve these desired outcomes.
Mortar and Grout Overview
Cementitious mortars have been widely used since the times of the ancient Greek and Roman Empires and have remained a fundamental building material in the 2,000+ years since. Mortars are mixed materials made up of several basic ingredients. Cement (i.e., Portland Cement, Masonry Cement, Mortar Cement, etc.) is used for bonding, strength, and durability. Hydrated Lime is used for workability and water retention. Appropriately graded aggregates that generally constitute a majority of the mix are used for bulk and body, strength, and shrinkage resistance. There may also be some admixture ingredients added to address specific performance enhancements for an installation. Water is added in an appropriate amount to mix these ingredients together and initiate a chemical reaction that bonds everything together, including the bonding of masonry or stone materials.
While the formulations and mixes of the ingredients have varied somewhat in different times and places, the essential uses have remained fundamentally the same. In structural applications, mortar is used to hold stacked structural masonry (CMU, brick, stone, etc.) in place and contribute to the structural stability of the assembly. Generally, the mortar has less compressive strength than the units being held in place depending on the ratio of different ingredients and their specific characteristics. Regardless, such structural mortar has been the fundamental basis of the design and construction of buildings that use stone, brick, and other masonry products for structural walls.
Mortar is also used in non-structural applications to adhere thinner products (i.e., thin stone, masonry, tile, or manufactured concrete products) to the surface of a structural system that is already in place. An additional material may or may not be provided to create a smooth substrate (cementitious scratch coat, cement board, etc.) before the surface products are applied. The applied, thinner surface products are referred to as a veneer in this case and the mortar serves to adhere the veneer to the prepared substrate.
Pointing Mortar, sometimes referred to as joint grout are terms used for mortar that serves as a finishing material. Rather than using it to adhere materials together, it is primarily used to fill gaps, joints or other separations of thin masonry units. Its purpose is generally to seal the openings and create a more uniform surface that not only looks more finished, it also helps to keep out weather, dirt, debris, and other things that are less than desirable in construction.
For purposes of this course, we focus on the adhered application of thin masonry veneer which has become increasingly more common in design and construction compared to structural, heavier load, applications. In this context, there are three ways mortar is used in veneer applications:
- Scratch coat: Before a thin veneer material can be applied to a wall, a layer of mortar that is textured with a trowel (i.e., “scratch” the surface) may be applied evenly over the substrate, particularly if that substrate surface is at all irregular or uneven. Many veneer products require a metal lath to be incorporated as part of the substrate, so the scratch coat is commonly installed over that and any fasteners that hold it in place. This all makes it easier, in many cases, for the thin veneer to be applied properly once the scratch coat is solidified.
- Bond coat: Whether a scratch coat is needed or not, the veneer material needs to be bonded to the prepared surface with an appropriate mortar. This bond coat may be applied directly to the wall or applied onto the back side of each piece of veneer material and pressed into place.
- Pointing mortar: Some mixes are also designed and specified, with or without colorant, to be used for filling the gaps or joints between the thin masonry veneer units. This mortar is intended to fill all the gaps and seal the surface of the wall where it is being applied.
Each of these types of mortars can have variations in the way that they are mixed and the ratio of the different ingredients used to suit the needs of residential and commercial construction.
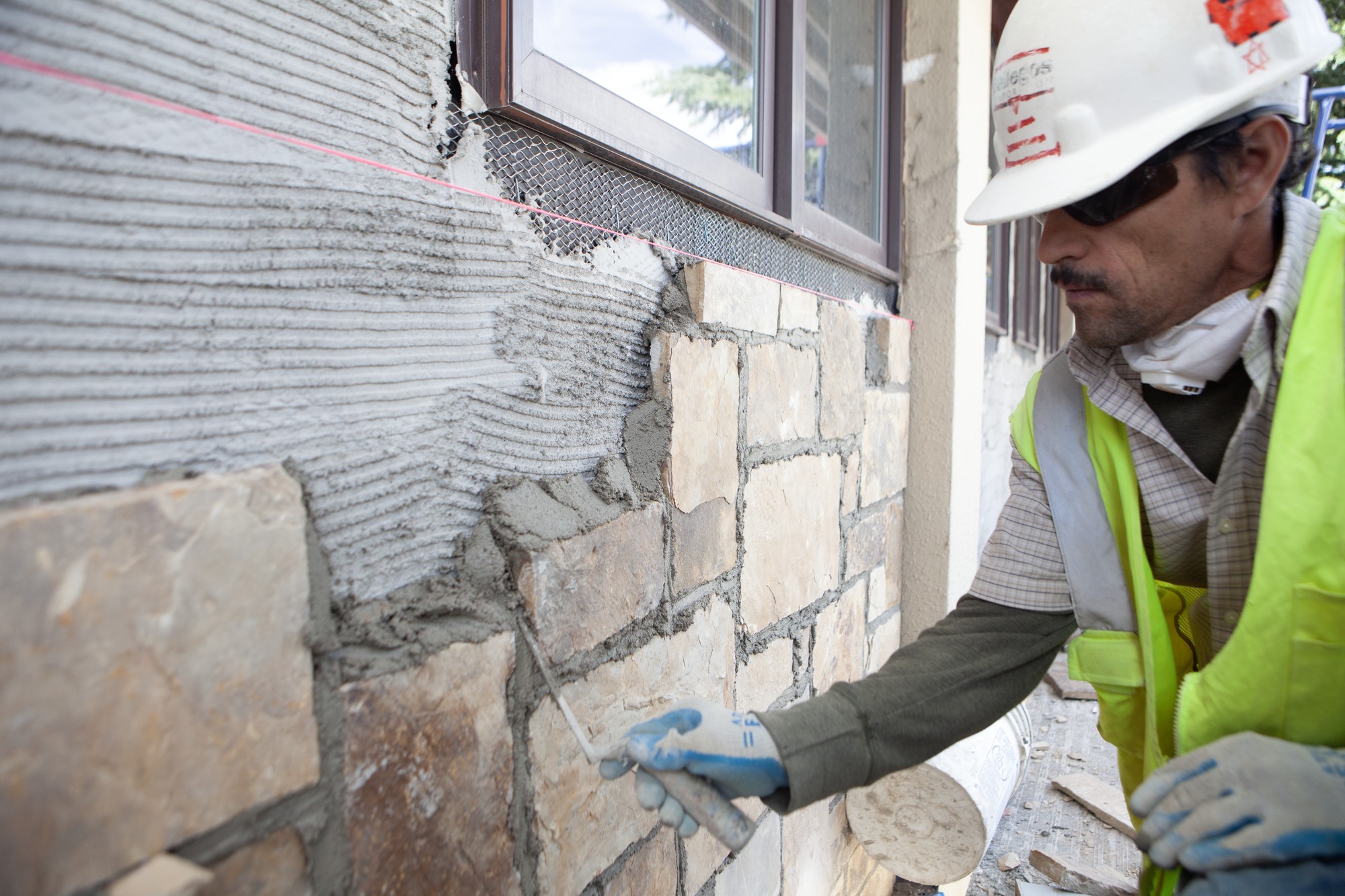
Photo courtesy of SPEC MIX
Mortar is needed for a scratch coat to prepare the substrate and for a bond coat to adhere the veneer product to the wall.
MORTAR MIXING
As already noted, mortars of all types require proper proportioning and mixing of the basic ingredients to produce the needed type of material. For best results, it is imperative that the proper ratios of each ingredient are maintained, or else different results may occur in terms of strength, durability, and general performance.
Site-Mixed Mortar
The traditional means to mix mortar ingredients has been to have bulk materials delivered to the construction site and shoveled by hand into a mechanical mixer. There are some obvious limitations to this approach since the mixing is completely dependent on the skill and understanding of the field worker(s) carrying out that mixing. Those hired to do the mixing may not be the most skilled workers, rather they are often the newest or youngest workers who are overseen by others who are focused on other tasks. Regardless, the quality of the mortar is dependent on the proper mixing of ingredients which also needs to be consistent between batches across an entire workday and project. This can be compromised by the fact that hand mixing is truly tiring work with heavy lifting, twisting, and turning all required.
Beyond the human factors, the outdoor conditions where mortar is mixed can have a significant impact on the quality. The ingredients, first and foremost, need to be protected from weather, which is commonly achieved with tarps over materials placed on the ground, particularly for sand. However, that doesn’t address airborne water vapor which can increase the moisture content of the sand beyond desirable levels or the moisture content of the sand when delivered to the jobsite from the supplier where it is not protected and often washed with water in the production process. It is also quite possible that ingredients placed on the ground can become readily contaminated with dirt or salts—things that can damage the mortar and contribute to unwanted efflorescence on the face of the finished product. Efflorescence is known to occur when water is present in the wall system, soluble salts are in the mortar or the masonry/stone/concrete units, and static pressure is present causing the water to migrate through the units and bring the salts to the surface. The storage of sand and other mortar ingredients on the ground for mixing can’t guarantee that soluble salts won’t contaminate the mix and later cause efflorescence or staining of the surface.In short, very strict quality control on the storage and protection of the ingredients is equally as important as quality control of the people doing the mixing and preparation of the mortar.
Pre-Mixed Mortar
The preferred alternative to site-mixing is to have mortars preblended in controlled conditions in a factory. Factory preblended masonry mortars eliminate most of the quality control issues and inconsistencies related to both worker skills and outdoor conditions. That’s because the mixing is carefully controlled using computerized equipment that measures the weight and volume of each of the ingredients to be sure the proportions are correct for the intended type of mortar being produced. By storing the ingredients either inside a factory or weather-tight silos, site conditions, weather, moisture issues, and efflorescence-causing soluble salts are controlled or eliminated.
Overall, the pre-blended mortar follows a tightly controlled mixing process meaning that the end products can be very consistent from one batch to the next and can be readily replicated if more is needed at a later time. This consistency applies not only to the makeup and performance qualities of the mortar but also to the color—clear concern if it is visible in the final form either as a grout or exposed mortar joint. Once the desired quantity is mixed, it is bagged in weather-resistant packaging and shipped to the construction site. Bag sizes can be anywhere from 50 pounds to 3,000 pounds for efficiency. Once delivered, the appropriate amount of water and final mixing is all that is needed for it to be ready to use.
Factory preblended mortars can be selected from standard offerings or custom-designed and produced to match or meet nearly any color or performance requirement specified. The cost for factory preblended masonry mortars and grouts can vary but are often ultimately the same (or sometimes more cost-effective) as jobsite mixed materials due to increased yield from the materials used and real on-site labor savings. The biggest benefits of preblended products overall, however, are greatly improved quality control and consistency across a project, i.e., truly meeting the specifications. Masons appreciate consistency since that makes their work look and perform better while making it easier to use than site-mixed products.
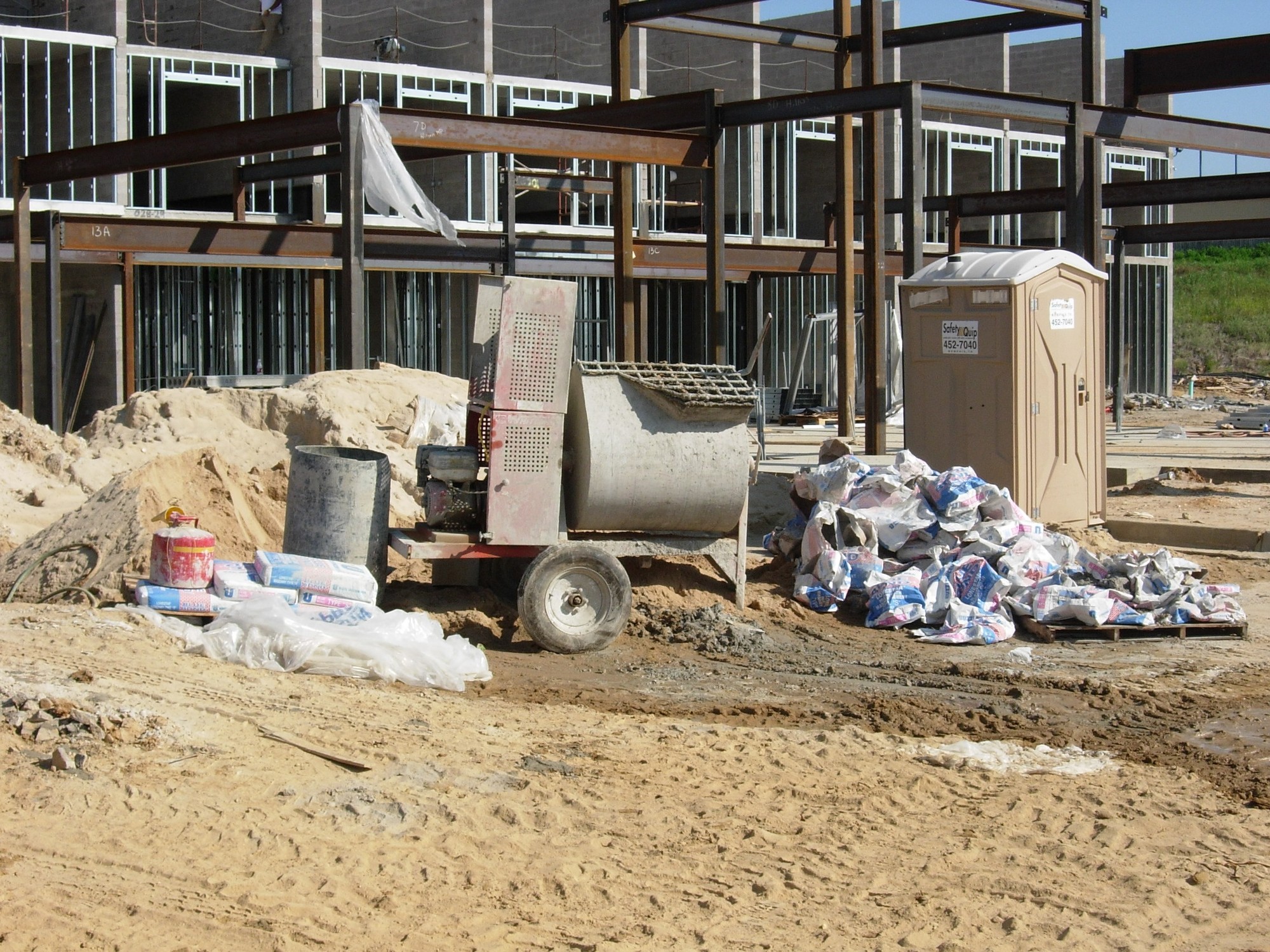
Photo courtesy of SPEC MIX
There are two ways to make mortar—field mixed outside on a jobsite with local labor or preblended in a factory with skilled workers and computerized equipment for complete quality control.
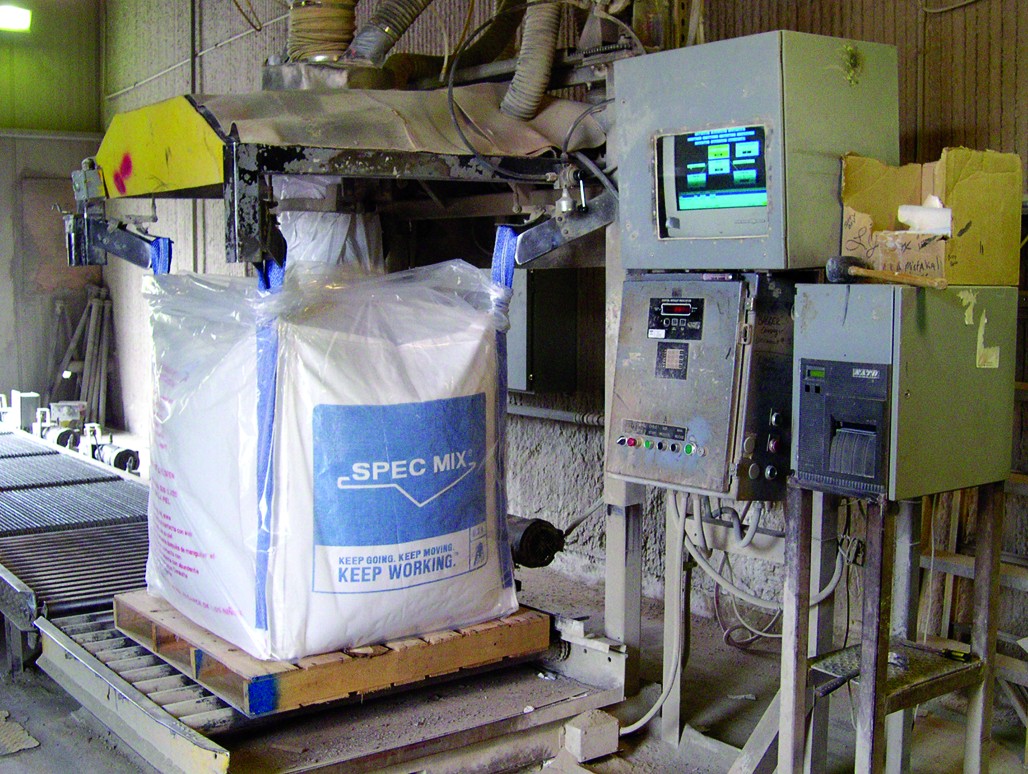
Photo courtesy of SPEC MIX