Versatility of Design and LEED Certification with Metal Composite Materials
The critical attributes attained from the MCM production process are bond strength and flatness, making the panels aesthetically superior even after years of exposure. Based on many millions of square feet of experience, it was determined that a specific bond strength, both as-manufactured and after controlled exposure, was adequate to ensure that a panel would remain bonded over time. This performance value has been incorporated into the requirements used by major manufacturers and certification agencies to evaluate the acceptability of the finished MCM. Flatness is also a significant desired and sought-after property for MCM exterior cladding. This is defined in a white paper by the Metal Construction Association titled: “Visual Acceptance Parameters for Metal Composite Material (MCM) Panels and Panel Systems.”
FEATURES, BENEFITS, AND ADVANTAGES OF METAL COMPOSITE MATERIALS
Architects can choose from many cladding materials available in today’s market, so why choose metal composite material? This section provides an overview of the attributes and benefits of MCM. It is important to note that the material is created by a manufacturer and then fabricated for a project by a fabricator. The discussion begins with a notable project where metal composite panels figured into its LEED certification.
Anatomy of a LEED Project: Boston University Center for Computing & Data Sciences
The LEED Platinum-certified Boston University Center for Computing & Data Sciences, designed by Boston Architect KPMB, provides an exceptional workspace in a building that demands attention. Across 19 floors in 345,170 square feet, the $305 million center defies convention, forming an iconic landmark in the Central Campus. The cutting-edge design incorporates remarkable architecture, state-of-the-art resources, an environmentally friendly approach, and spacious, adaptable learning spaces.
The new center at Boston University is one of the greenest buildings in Boston, boasting 100 percent fossil fuel-free energy and unmatched energy efficiency. Designed to encourage collaboration, it delivers on its promise to students, faculty, researchers, and the environment.
The exterior profile captivates with cantilevers that soar above the campus and the Charles River, resembling a towering pile of books, as described by the leadership of Boston University.
Specialized Metal Fabricators fabricated, and Ferguson Neudorf Glass installed, 88,291 square feet of metal composite material in a bright mirror finish and a custom russet pearl finish to achieve both aesthetic and performance targets. The material is lightweight and durable, and consists of coil-coated and anodized aluminum sheets laminated on both sides of a fire-retardant core material. It is highly formable and integrates seamlessly into curtain walls, providing an ideal solution to this boundary-pushing build.
The anodized mirror finish offers the same reflective qualities, brightness, and transparency as conventional mirrors while being unbreakable and much lighter than glass or acrylic, and highlights the distinctive architectural features of the much-discussed exterior.
The project earned its platinum rating in LEED BD+C: New Construction under LEED v4. The credits that may pertain to its MCM content include:
Category: Material & Resources
- Building life-cycle impact reduction: 3 points of 5 possible
- Building product disclosure and optimization - environmental product declarations: 1 point of 2 possible
- Building product disclosure and optimization - sourcing of raw materials: 1 point of 2 possible
- Building product disclosure and optimization - material ingredients: 2 points of 2 possible
- Construction and demolition waste management: 1 point of 2 possible
Category: Innovation
- Innovation: 5 points of 5 possible
(For an accounting of all points earned, go to: https://www.usgbc.org/projects/boston-univ-computing-data-sciences?view=scorecard.)
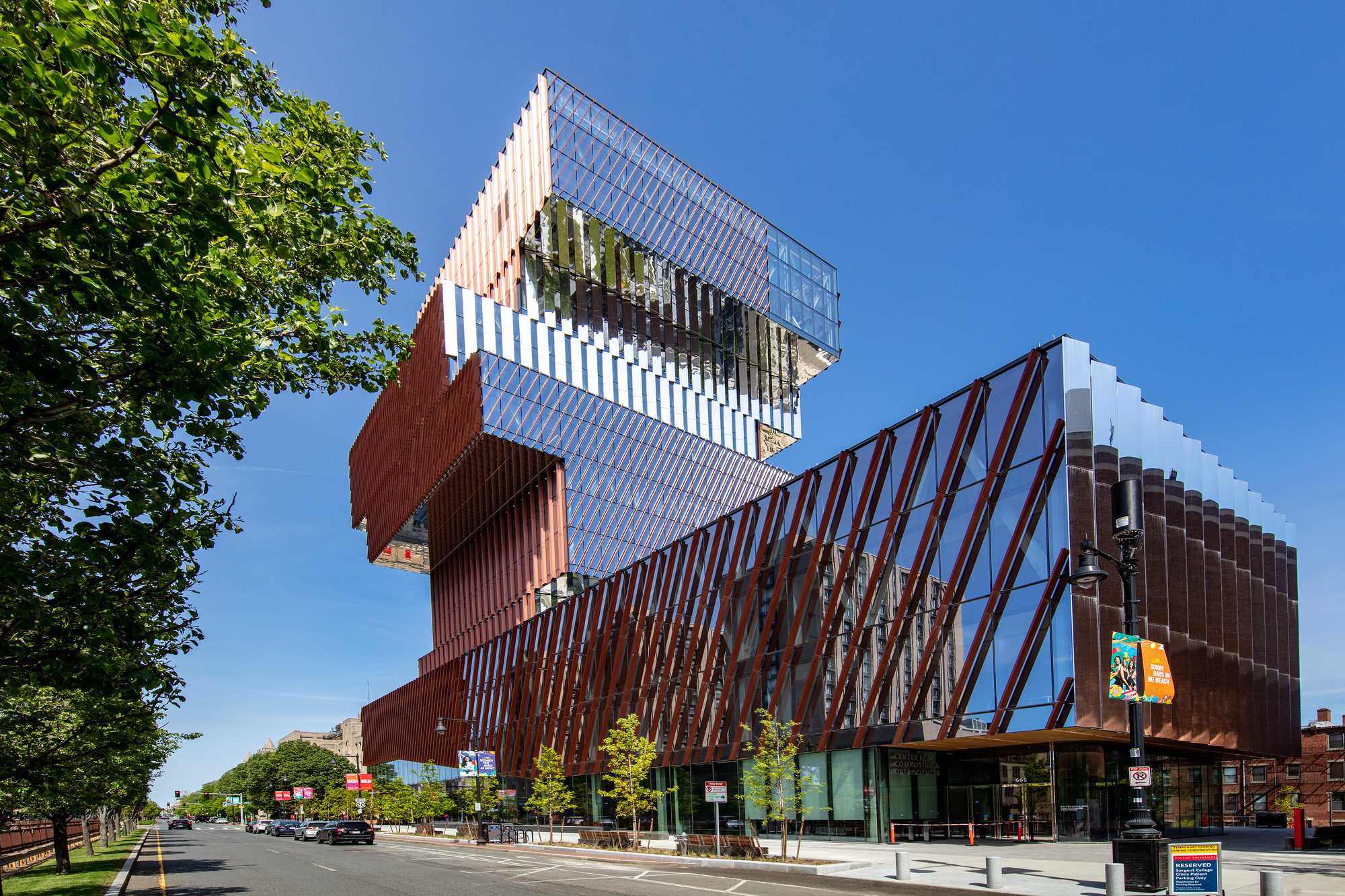
Image by Bob Perzel Photography
Boston University Center for Computing & Data Sciences, designed by Boston-based KPMB Architects.
MCM BENEFITS AND ATTRIBUTES
The specification of MCM brings these benefits and attributes:
Formability Inspires Creative Designs
Being formable and versatile, metal composite materials can achieve sweeping curves and tight radiuses and can perfectly adapt to a building’s contours. Brick, stone, and wood cannot be shaped with the same ease. Because of these attributes, MCM encourages innovative architectural design.
Lightweight
MCM is lightweight and thus is easier to transport and handle on-site. It places a reduced load on the wall framing and foundation (brick, stone, and solid plate weigh more). The lightweight MCM reduces the dead loads on structural members, saving construction costs.
High Rigidity
MCM also provides high rigidity. Due to its composite structure, it achieves a high strength-to-weight ratio, allowing for large panel sizes. It is durable, stable, and can be perfectly formed without any loss of rigidity.
Oil Canning
MCM panels keep their shape and remain flat, even when exposed to extreme temperature changes. Flatness is critical; architects must specify the correct material to avoid oil canning. The degree of oil canning and the appearance of the sheets will vary depending on factors such as the length and color of the panels, alloy, gauge, galvanizing process, substrate condition, and exposure to sunlight. Metal composite material panels are naturally flat and provide the lowest risk of oil canning.
Reflective
MCM is reflective (of both heat and light), potentially reducing the thermal loading on a building. Special “cool” paint finishes can increase this reflectivity.
Weather/Corrosion Resistance
MCM does not degrade in harsh environments. Select finishes inhibit corrosion in the harshest conditions, such as along coastlines with wind-driven salty air vapor.
Affordable
Large panel sizes and prefabricated panels provide fast installation at a lower cost. Depending on the project location, complexity, panel sizes, and attachment system, the estimated installed cost ranges from $30 to $80 per square foot.
Temperature Resistive
MCM products withstand environmental temperature changes from -55 to +175 degrees °F (-50 to +80°degrees Celsius). The coefficient of linear expansion is governed by the aluminum sheet. A 10-foot panel could expand 3.5 millimeters or 0.14 inch over a 90-degree°F temperature range.
Perforation
MCM has perforation capabilities. Perforation patterns can be geometric, slotted, or customized. Holes may be punched or routed by computer numerical control (CNC). Perforated panels are ideal for a variety of applications, including parking garages. Note that perforation is not the MCM manufacturer’s responsibility or capability, but it belongs to the fabricator.
LEED Project: MCM Panels Help Bring About a Unique Design Serving a Purpose
Chicago is renowned for its skyscraper architecture, and the city’s LEED Gold-certified Tower Hospital at Rush University Medical Center, designed by Chicago-based Perkins+Will, stands tall among the best. Rush University and the city of Chicago praise the new 840,000-square-foot project. It has won numerous awards and accolades, including Engineering News-Record Midwest’s Project of the Year (2012) and the 2013 MCA Chairman’s Award in the Institutional Project category. KPMG named the Rush Tower “one of the most innovative and inspiring urban architecture projects in the world.” The Chicago Tribune architectural critic Blair Kamin called it a “towering achievement; the new Rush Hospital could be Chicago’s next great building.”
More than just a pretty building, it was designed by and for its occupants—the doctors, nurses, staff, and patients who use it. The unique butterfly-shaped design is awe-inspiring to outsiders, but the design also serves a practical purpose. The floor plan, essentially a triangle, brings the patient rooms closer together, a specific concern for the nurses seeking more efficient access to patients. “We used an inside-out approach to design Tower Hospital,” said John Moorhead, senior project designer at Perkins+Will.
The architects collaborated with Rush staff to find out how they worked and designed the shape of the building to fit their operational model. “We let that impact what the design needed to be,” Moorhead said. “The nurses talked about the number of miles they walk per shift. They were particularly interested in creating a plan that pushed together the patient rooms.”