Greener Building Materials
VOC CONTENT, EMISSION TESTING AND STANDARDS
When a manufacturer, a design professional, a building owner, or even a consumer wants to know the VOC content in a paint or coating product, the information is typically available on the product label, technical data sheets, and often in the safety data sheets. For more detailed VOC content information and for third-party verification of that data, it is most effective to review the results of an analytical test. The standard way to do this is to identify the VOCs used, and then determine the weight of the VOC solvents (usually measured in grams) that exist in a specific volume (a liter) of product solids. Note that water and exempt compounds are not included, rather it is the grams of VOC divided by the volume of formulation solids measured in liters. The result is shown in grams per liter (g/L).
There are several well-established and widely accepted methods for testing the presence of VOCs in materials and products.
- EPA Test Method 24 “Determination of Volatile Matter Content, Water Content, Density, Volume Solids, and Weight Solids of Surface Coatings.” This method is applicable for the determination of volatile matter content, water content, density, volume solids, and weight solids of paint, varnish, lacquer, or other related surface coatings. It relies on a number of ASTM standards to be used and the testing process to be carried out as prescribed. They establish a “non-detect” level based on the testing, but it has been considered by some in the industry as unreliable for coatings with VOC content of below 100 g/L.
- ASTM D 6886 “Standard Test Method for Determination of the Weight Percent Individual Volatile Organic Compounds in Waterborne Air-Dry Coatings by Gas Chromatography.” This testing procedure is considered to be more accurate than EPA Test Method 24 since it relies on a different type of testing apparatus and process. It is the most favorable and widely used test for VOC content determination.
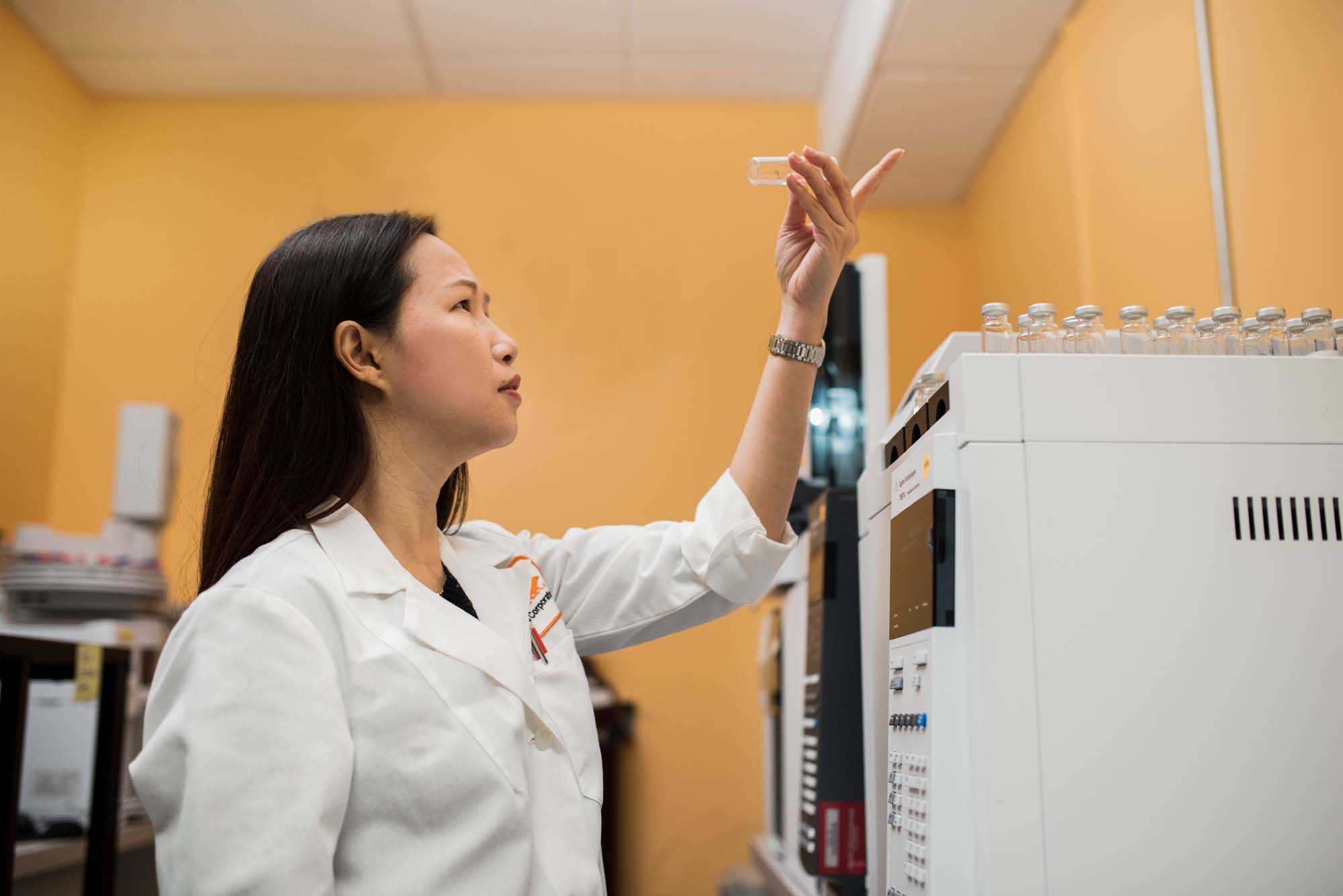
Photo courtesy of Behr Paint Company
The testing of paints and coatings for VOC content and emissions can be done following a variety of test methods and standards, although they differ in their techniques, applicability, and requirements for achieving “low-VOC” or “zero-VOC” status.
Once testing is complete on products, the test results can be applied to relevant standards that determine the appropriate levels of VOCs based on the category of usage. While EPA standards are national, other states have enacted or adopted their own rules and regulations concerning different types of VOCs and other pollutants. Some of the commonly referenced standards include the following:
- South Coast Air Quality Management District (SCAQMD) Rule 1113 California’s South Coast AQMD’s Governing Board adopts policies and regulations that promote clean air within its four-county area of Southern California (the District), the smoggiest in the nation. Rule 1113 is the rule for VOC levels by category which references test methods such as ASTM 6886, Method 24, and others. It is based on federal and state law which requires that South Coast AQMD achieve clean air standards to protect public health. As stated, “This rule is applicable to any person who supplies, sells, markets, offers for sale, or manufactures any architectural coating that is intended to be field applied within the District to stationary structures or their appurtenances, and to fields and lawns; as well as any person who applies, stores at a worksite, or solicits the application of any architectural coating within the District. The purpose of this rule is to limit the VOC content of architectural coatings used in the District.” This comprehensive program requires an Annual Quantity and Emissions report with fees as established in SCAQMD Rule 314. The report must indicate testing following a number of ASTM standards and show compliance with the maximum levels of VOCs in the products used or sold in the District. This rule also sets levels for low- and zero-VOC products including coloring (pigment) agents.
- The Lake Michigan Air Directors Consortium (LADCO) This multi-state consortium was established in 1990 and currently includes the States of Illinois, Indiana, Michigan, Wisconsin, and Ohio. Their main purpose is “to provide technical assessments for and assistance to its member states on problems of air quality, and to provide a forum for its member states to discuss air quality issues. LADCO’s major pollutants of concern are ozone, fine particles, regional haze and their precursors.” The program includes recommended rules for paints and coatings.
- The Ozone Transport Commission (OTC) This group was created under the Clean Air Act as a multi-state organization. They are “responsible for advising the EPA on developing and implementing regional solutions to the ground-level ozone problem in the Northeast and Mid-Atlantic regions. The OTC brings together the states from Virginia to Maine to coordinate reductions in air pollution that benefit the whole region.” They provide “air pollution assessment, technical support and a forum through which states can work together to harmonize their pollution reduction strategies.” Their voluntary rules include rules for paints and coatings.
- UL GREENGUARD The UL GREENGUARD Certification program has established standards and emission limits for a variety of product groups, including building materials such as paints and coatings. Note that VOC testing is different than emissions testing; they are related but not identical. Some components within a product formulation can show up as a VOC in the product testing but not show up in the emission testing because they react with the coating film during drying. The EPA and the state of Washington initially used UL GREENGUARD Certification emissions limits as purchasing specifications for furniture and commercial building products. The UL GREENGUARD Gold Certification Standard includes health-based criteria for additional chemicals and requires lower total VOC emissions levels to ensure that products are acceptable for use in environments such as schools and healthcare facilities. In addition to limiting emissions of more than 360 VOCs and total chemical emissions, UL GREENGUARD Gold Certified products must also comply with the requirements of the California Department of Public Health (CDPH) Standard Method for the Testing and Evaluation of Volatile Organic Chemical Emissions from Indoor Sources Using Environmental Chambers, also known as California Section 01350. All certified products are subject to a review of the manufacturing process and routine testing to demonstrate minimal impact on the indoor environment in the long period.
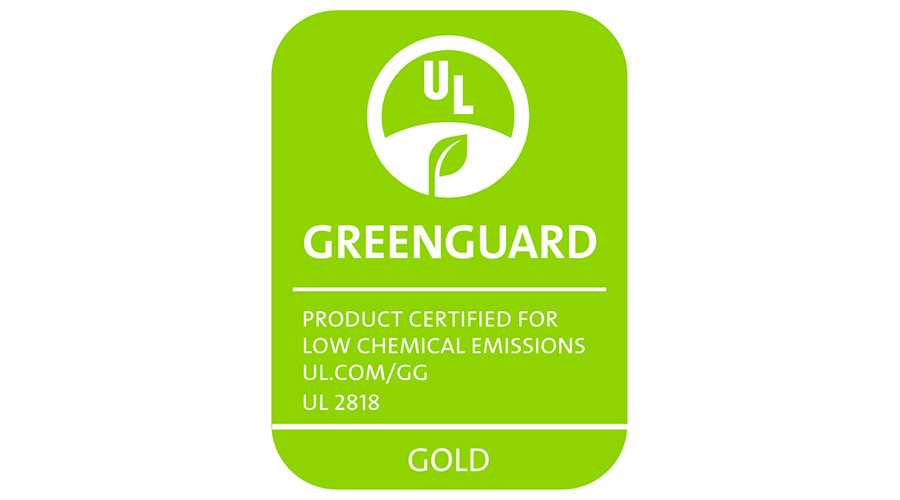
Image Source: UL Solutions
The UL GREENGUARD Gold label is awarded to products that have been independently tested and verified to meet specific requirements for VOC content and other criteria. GREENGUARD is a registered trademark of UL LLC. For more information, visit ul.com/gg.
Regardless of the test methods or standards used, the intent is to independently verify both the VOC content of paints and coatings as well as the potential for emissions once the products are applied inside a building. Once the levels are determined, then the appropriate designation of low-VOC or zero-VOC can be considered. If the products meet other criteria, then they can be certified under the UL GREENGUARD program.
DESIGNING FOR HEALTH: STRATEGIES TO MINIMIZE VOC EXPOSURE IN BUILDINGS
In the interest of designing healthier indoor environments, there are a number of things to take into consideration related to VOCs and other potentially harmful building materials and ingredients. The first step is to recognize the importance of the issue and then take steps during the design process to seek out ways to reduce or eliminate these potentially harmful materials and ingredients. This includes reviewing available data on products and consideration of following green building standards that promote health and wellness. All of these points are reviewed next.
Impacts of Poor Indoor Environmental Quality
According to the EPA, “The ability of organic chemicals to cause health effects varies greatly from those that are highly toxic to those with no known health effect. As with other pollutants, the extent and nature of the health effect will depend on many factors including level of exposure and length of time exposed.” That is all fair and true, but there are some common health symptoms that have been experienced soon after exposure to some VOCs according to the EPA. These include eye and respiratory tract irritation, headaches, dizziness, nausea, fatigue, visual disorders, and memory impairment. Long-term health effects can include damage to the liver, kidney, and central nervous system, and even cancer in some cases.
As individuals experience any of the above symptoms, the broader impacts on a school, company, organization, etc. have been investigated by numerous sources often cited by the U.S. Green Building Council and others. Among the common findings based on EPA reports are lower productivity, higher absenteeism, lower testing scores, and higher rates of disease and illness. Clearly, these all can significantly change the success of any of the groups of people affected by poor indoor environmental quality, particularly from VOCs. Fortunately, there are ways to avoid these issues if design and construction professionals pay attention to them.
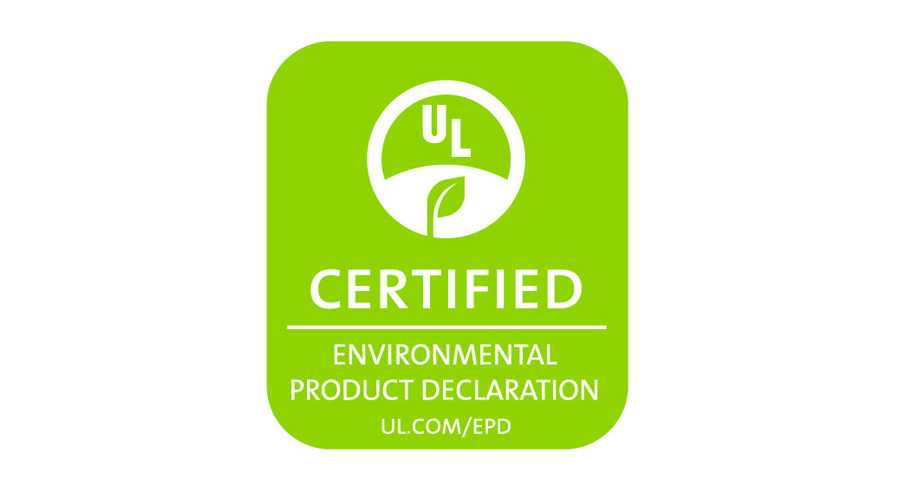
Image Source: UL Solutions
Environmental Product Declarations are available on a wide range of products and can be used to enable the comparison of environmental impacts of like products, providing increased transparency.