Greener Building Materials
Learning Objectives:
- Comprehend what volatile organic compounds (VOCs) are and their sources in architectural coatings.
- Identify the environmental and health effects of VOCs in indoor and outdoor environments.
- Evaluate the regulatory standards governing VOC content in architectural coatings.
- Recognize sustainable alternatives to traditional high-VOC coatings and their benefits to people in the built environment.
- Learn best practices for specifying low- and zero-VOC coatings in design and construction projects.
Credits:
This course is approved as a Structured Course
This course can be self-reported to the AANB, as per their CE Guidelines
Approved for structured learning
Approved for Core Learning
This course can be self-reported to the NLAA
Course may qualify for Learning Hours with NWTAA
Course eligible for OAA Learning Hours
This course is approved as a core course
This course can be self-reported for Learning Units to the Architectural Institute of British Columbia
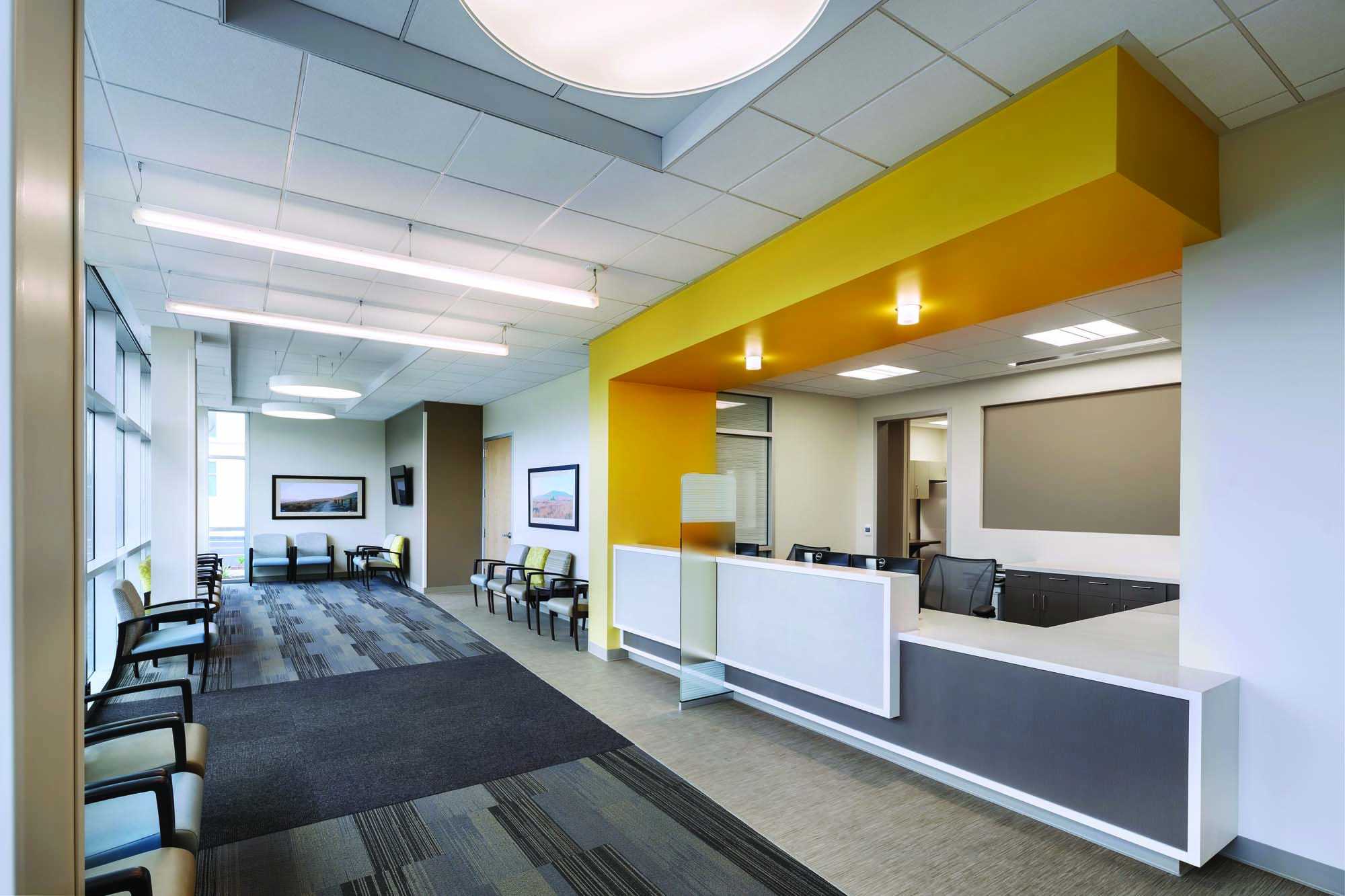
Photo courtesy of Behr Paint Company
The quality of indoor environments in buildings of all types is directly impacted by the choice of products used in those spaces, including paints and coatings.
The green building movement in the U.S. has brought attention to the quality of indoor environments, focusing on factors like lighting, thermal comfort, acoustics, access to daylight and views, and air quality. A key aspect of indoor environmental quality is the choice of building materials, especially those that can release harmful chemicals, such as volatile organic compounds (VOCs). According to the U.S. Environmental Protection Agency (EPA), “VOCs include a variety of chemicals, some of which may have short- and long-term adverse health effects.” In response, manufacturers have developed products with reduced or no VOCs while maintaining performance. As a result, green building standards like LEED™, WELL™, and the Living Building Challenge™ aim to minimize or eliminate VOCs in buildings and materials, including paints and coatings. Some states, such as California, have also set specific codes and testing standards to limit VOC exposure in materials. This course covers these VOC-related aspects in buildings, particularly in paints and coatings, to help architects and design professionals meet current standards and understand available product options.
UNDERSTANDING VOCS
The term volatile organic compounds (VOCs), refers to the chemical makeup of compounds that have high vapor pressure and low water solubility. This means that they easily evaporate at room temperature. The term “volatile” refers to this tendency to vaporize, while “organic” indicates that they contain carbon.
While VOCs also occur naturally in the environment (example: they are emitted by trees and vegetation) these natural sources pose little health risk due to the compound’s nature or their low concentrations. However, synthetic VOCs can be more harmful, especially if they accumulate indoors, because of their specific chemical nature and higher concentrations.
According to the U.S. EPA, “Many VOCs are human-made chemicals that are used and produced in the manufacturing of paints, pharmaceuticals, and refrigerants. Gaseous VOCs are emitted (also called ‘off-gassing’) by a wide array of products numbering in the thousands.” Common examples of such VOCs include formaldehyde, d-limonene, toluene, acetone, and ethanol. The EPA points out that “VOCs include a variety of chemicals, some of which may cause short and long-term adverse health effects.” Because the evaporated chemicals remain in the air and can be inhaled, exposure to VOCs is a health concern.
Specific to our purposes here, VOCs are present in a wide variety of finishing products such as paints, varnishes, stains, paint strippers, adhesives, furnishings, and other building materials. These products can release VOCs during use and also while stored indoors, leading to higher indoor concentrations - sometimes up to ten times higher than outdoor levels.
Limiting VOCs
VOCs have been studied extensively with generally accepted knowledge developed related to which ones are a concern and under what circumstances. For example, certain VOCs in the outdoor air, particularly those emitted from automobile exhaust, are a concern because they can cause the creation of excess ozone and lead to smog. Accordingly, the U.S. EPA has developed regulations to define outdoor air quality and help control smog.
In the same way, the indoor use and regulation of VOCs have been developed by the U.S. EPA and others. The application of those regulations depends on what is, or is not, classified as a VOC under those regulations. At the federal level, a VOC is not subject to scrutiny if the EPA designates it as “Exempt”, which it may do if testing determines it is not a significant concern. However, at the state and local level, a VOC can be exempt in one jurisdiction, but not another. Conversely, a VOC may be exempt for one purpose, but not for another purpose in the same jurisdiction.
A chemical can have a low vapor pressure and still be volatile in a coatings application, meaning it evaporates over time, even if slowly. However, it may not be classified as a VOC if it does not significantly contribute to ozone formation or air pollution under regulatory guidelines. This distinction is especially important for coatings manufacturers, as it influences compliance with environmental regulations while achieving desired coating performance.
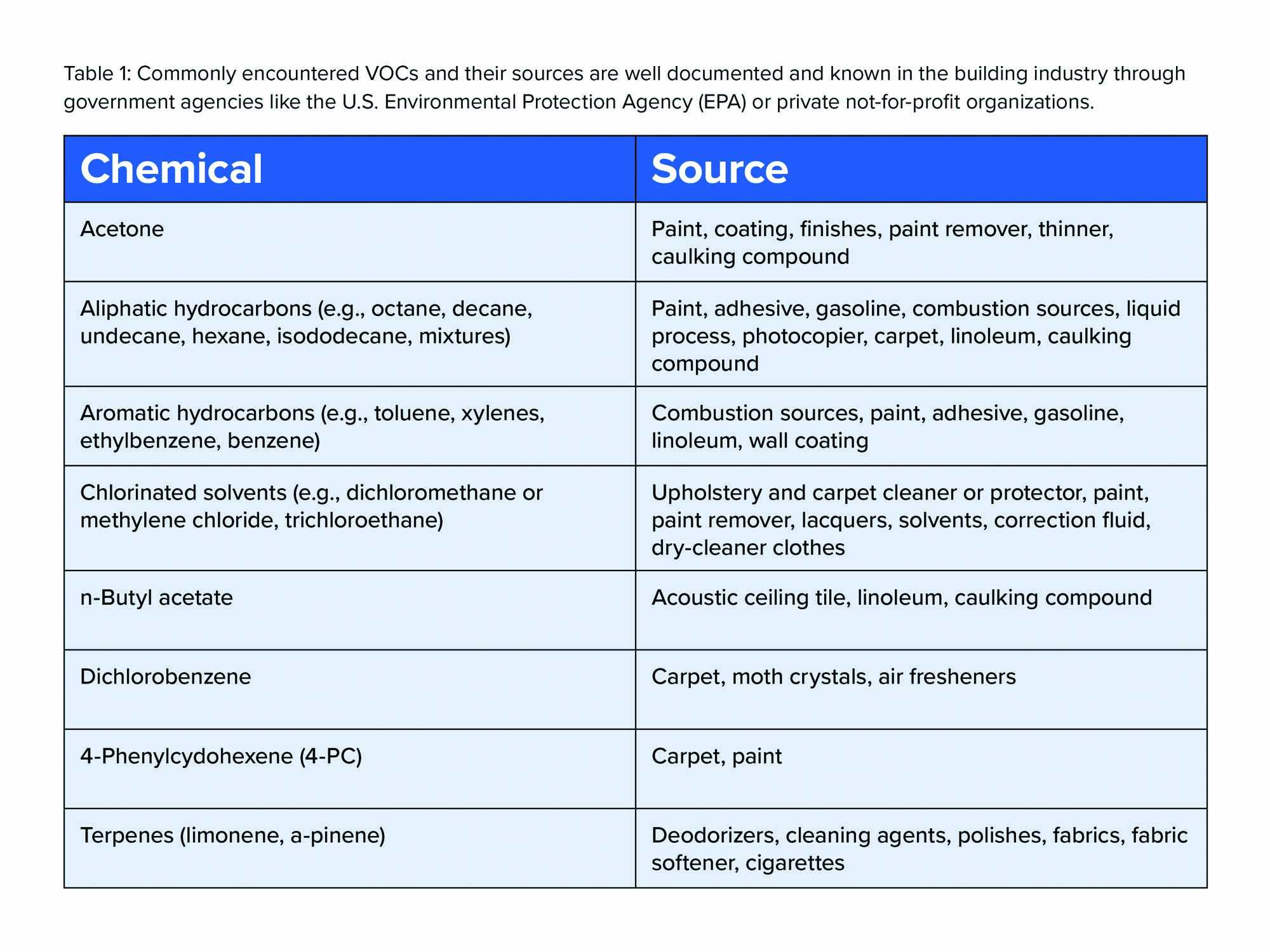
Source: Tucker, W.G. (2001) Volatile Organic Compounds (VOCs) Chapter 31. Spengler, J.D., McCarthy, J.F. and Samet, J.M., Eds., Indoor Air Quality Handbook, McGraw-Hill Companies, New York, 31.1-31.20.
Commonly encountered VOCs and their sources are well documented and known in the building industry through government agencies like the U.S. Environmental Protection Agency (EPA) or private not-for-profit organizations, such as the U.S. Green Building Council and the WELL Building Institute.
VOCs in Paints and Coatings
VOCs are commonly used in paints and coatings, primarily as solvents or thinners that are part of the product. These solvents work with components of paint products such as the binder to create desirable properties in paint. Because VOCs evaporate quickly and easily at room temperature, paint usually dries more quickly than without them. However, this isn’t always true since some VOCs have a lower boiling point than water and evaporate before water. Other VOCs have a higher boiling point than water and evaporate after water does.
The VOC solvents and thinners help keep the paint in liquid form until application. Once a container is opened and paint is applied, it is exposed to the air and the evaporating compounds move quickly throughout a room or space. The first evidence of that is the odor of fresh paint often associated with the process—people can smell the evaporated VOCs in the air. Removing the VOCs means removing some of the evaporative process and may increase the drying time. To help with that, controlling the indoor environment by keeping the room well-ventilated to reduce humidity and maintaining the temperature in the range of 70-90 degrees are usually recommended. Of course, different surface types may require different environmental conditions.
Another reason VOCs are used in paints and coatings is to improve adhesion and durability once the product is dry. The solvents work with the resin or binder to aid in film formation, which helps with performance and durability. Of course, different buildings and locations have different needs for durability. Residential painted walls are different than commercial painted floors for example. Therefore, different paints can be formulated for these different needs and conditions.
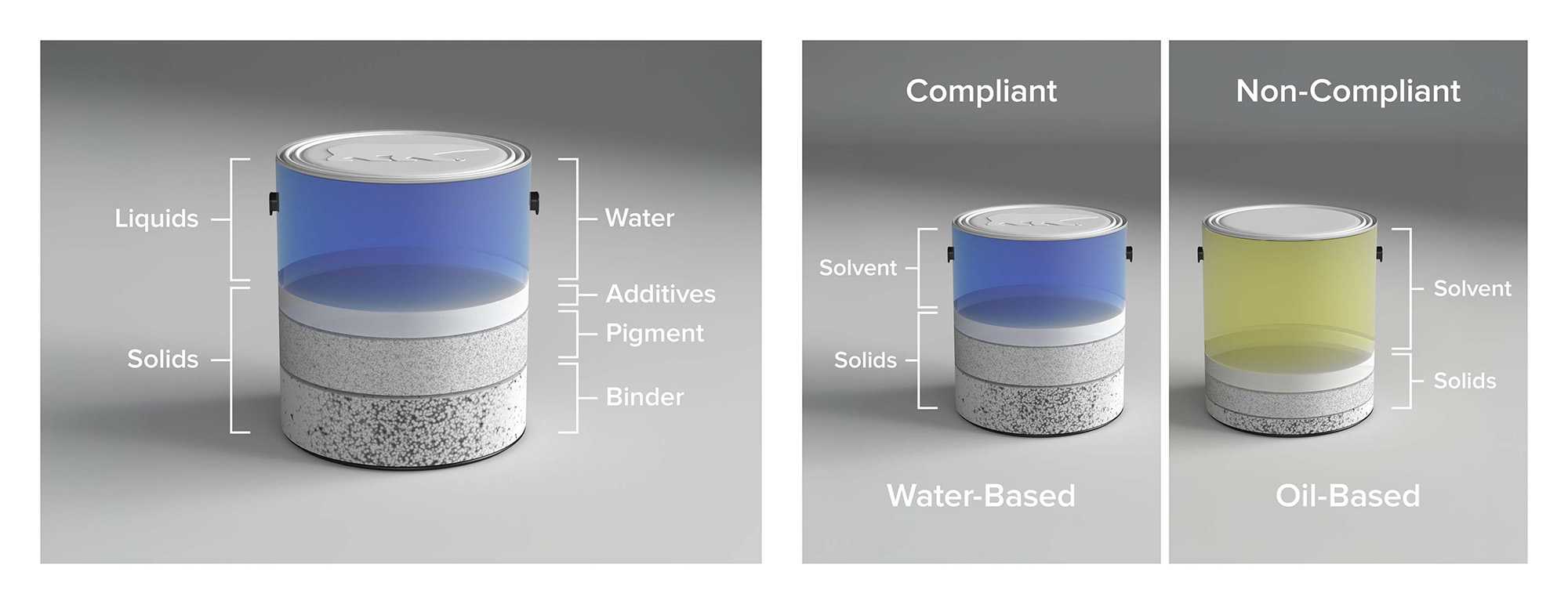
Photos courtesy of Behr Paint Company
Paint is typically made from solids such as pigment and binder plus solvents or thinners which may contain VOCs. Compliance with regulations and standards limits the amount of VOCs present in paints and coatings. Note that some solvents, such as water, are not VOCs and are not relevant to the regulations.
VOCs are also commonly used in paints because they can help focus the experience of paint application with improved flow and leveling of the paint. Similarly, they control the open time (i.e., workability time) and help control the drying time. In addition, coalescent compounds, which may contain VOCs, can allow the use of a harder resin based on a higher glass transition temperature (Tg)—the property of a resin that describes the temperature at which it changes from a hard, glassy state to a softer, rubbery state. This is useful to control in order to make a harder paint film that is more durable and resistant to scuffs, marks, and chemical interactions. Typically, lower VOC coatings are softer and not able to achieve the same hardness as high VOC coatings.
The paint and coatings industry has responded to the need for lowering the amount of VOCs in their products with many manufacturers offering choices that use a smaller amount of VOCs than typical products. Regulations have been developed that define “low-VOC” products which still contain some amount but reduce the exposure to people who are using them. The standard level used by LEED and others is a threshold of content that is less than 50 grams of VOC per liter. While low-VOC paint lines are widely available and used, they still may contain the chemicals mentioned previously. However, there are also “zero-VOC” paint products that are produced without adding any VOC chemicals to the paint mixtures resulting in a product that might only have trace amounts, if any, usually related to impurities in the raw material ingredients. Relatedly, depending on the colorant system used, additional VOCs may be added to the formulation during tinting.
“Zero-VOC” label products should have no intentionally added VOCs and contain no more than 5 grams of VOC per volume of solids present. The common product emission information found on “zero-VOC” paint labels typically indicates that they emit very low amounts of VOCs with most emissions occurring during painting and for 48 hours after. Some emissions may continue for two weeks or longer.
The architectural coatings industry continues to investigate ways to reduce if not eliminate any residual VOCs from existing low-VOC technologies. Additionally, the majority of research is focused on developing high-performance, water-based, low-VOC solutions for applications where oil-based coatings are typically specified.