Profiles in Multifamily Innovation
“The nice thing about aluminum is it offers lots of design flexibility in terms of look, color, and customization. These frames can incorporate easily with whatever rainscreen or exterior cladding system,” he points out. “We see projects today that allow tons of natural light, have operable windows to bring fresh air and improve indoor air quality, offer very wide views and all the while hit performance targets. The innovations in the fenestration industry today are amazing.”
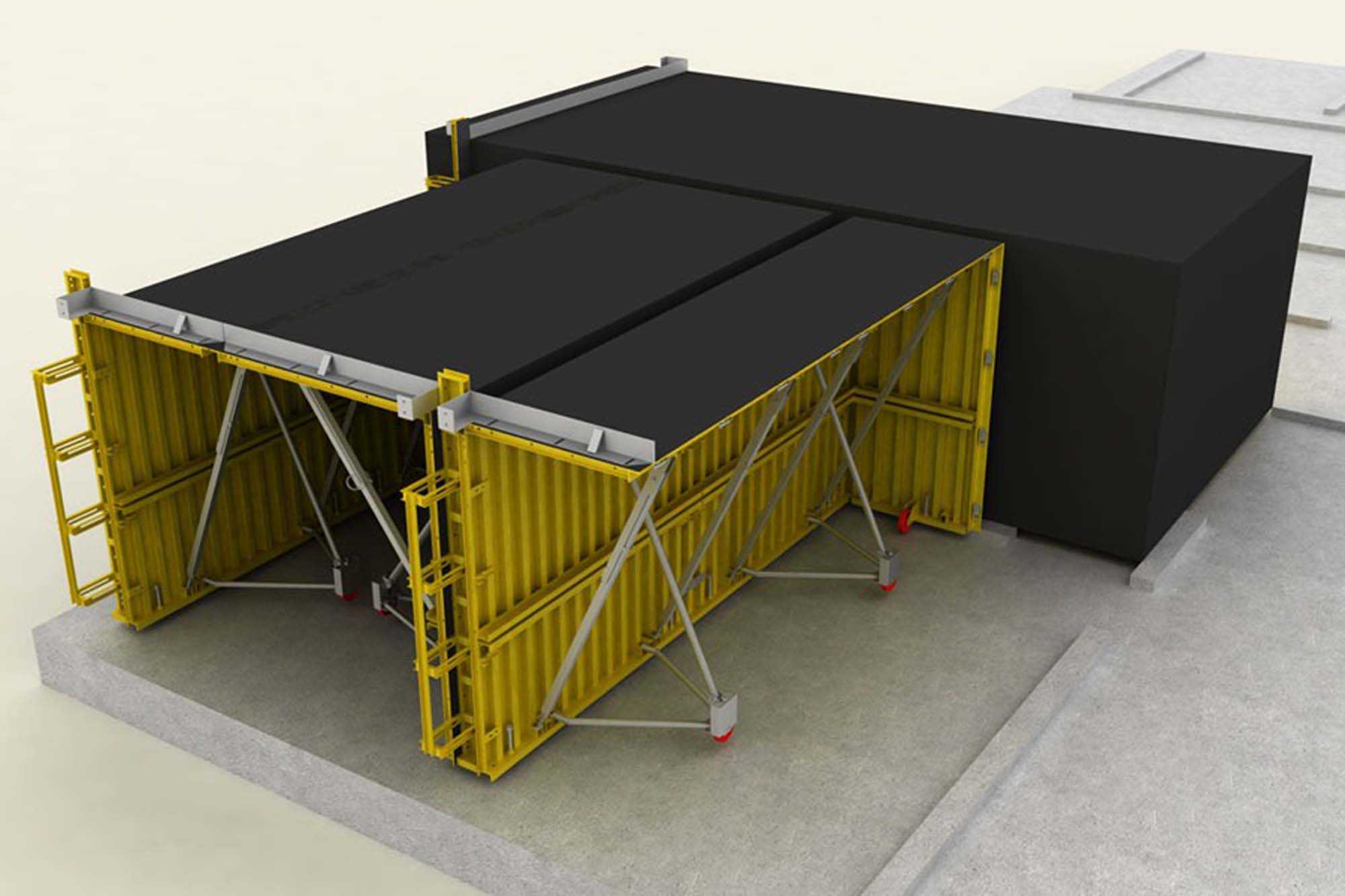
Photo courtesy of All Weather Architectural Aluminum
Thin-shell concrete tunnel-form system with modular aluminum formwork.
INNOVATIONS IN THE BUILDING PROCESS
In this article, innovations in multifamily design have so far focused on benefits to the occupant and building owner, but there have been significant steps forward in the construction of multifamily projects, as well. New onsite building systems that enable an efficient and repeatable building process, as well as the rise of modular off-site construction, both offer builders the opportunity to streamline the construction process like never before.
Building Better─Faster
Thin-shell concrete load-bearing tunnel-form systems crafted with modular aluminum formwork have greatly reduced the cost of construction and reduced build schedules to allow for more creative design options. This method involves creating monolithic concrete structures, where walls and slabs are cast simultaneously using modular aluminum formwork. The term “tunnel” refers to the shape and method used to form the concrete walls and slabs in one continuous pour. The tunnel-form system involves large, reusable formwork units that are shaped like half-tunnels or U-shaped molds. These molds, sometimes prefabricated to exact specifications, are positioned on-site to create both the vertical walls and the horizontal slabs of a building simultaneously, resulting in a monolithic concrete structure.
After the concrete cures, the formwork is removed and reused for the next section, advancing through the building floor by floor. The formwork system allows for rapid construction and increased accuracy in creating durable and consistent structural elements.
Before the advent of thin-shell concrete load-bearing tunnel-form systems, traditional construction methods for low-rise multifamily buildings typically relied on a combination of reinforced concrete frames and masonry infill, steel frames with cladding systems, or stud framing using wood or steel.
While reinforced concrete or steel frame systems provided a solid structural frame, they required longer construction times due to the need for multiple stages of framing, masonry work, and finishing. In addition, traditional non-insulated concrete systems were more prone to thermal bridging, leading to an overall increase in energy consumption for heating and cooling. Construction methods onsite were also often wasteful, generating more debris and requiring more material compared to modular systems used in modern tunnel-form methods.
The use of modular aluminum formwork ensures precision in construction, which minimizes gaps, cracks, and thermal bridges that can lead to energy loss. As the formwork is reusable, it reduces construction waste and supports environmentally friendly practices. Because the forms are aluminum, they are durable, lightweight, and 100 percent recyclable at the end of life. These systems also allow for better integration of modern insulation materials, further improving the overall energy efficiency of the buildings.
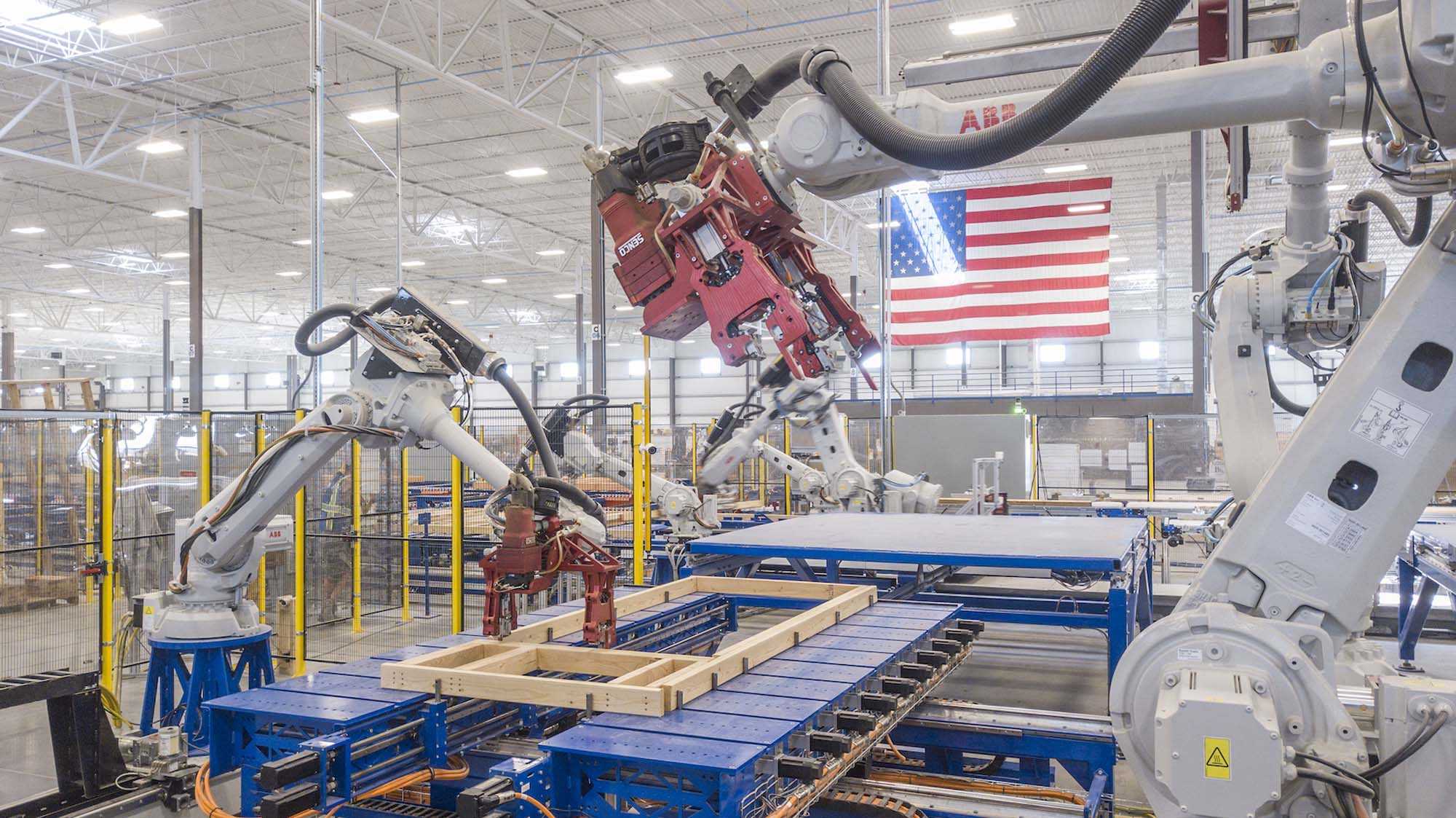
Photo courtesy of Autoval
Automation and robotics in panel manufacturing facilities have reduced both construction schedules and call-back issues.
The rise of Automation
An important advancement in multifamily construction is the automation of prefabricated and panelized facade systems. This innovation allows manufacturers to streamline the production of factory-built panels, enhancing both the speed and thermal efficiency of construction. The result is a significantly shorter construction timeline, reduced dependency on skilled labor, improved quality control, increased safety, and more efficient integration of materials like aluminum into building envelopes or rainscreen systems.
For the architect, the process of designing prefabricated panels enables a great deal of creative expression in the facade while also supporting performance goals and helping the builder. Panels come pre-assembled with key elements such as moisture barriers and exterior finishes thanks to advanced manufacturing techniques. This approach offers less reliance on weather conditions and a more predictable construction timeline, minimizes on-site labor, and ensures that the building components meet high-performance standards.
While offsite construction of building components has been around for decades, most notably in framing systems, one major innovation to the process has been the inclusion of robotic or automated panel manufacturing.
An advantage of robotic automation is its ability to reduce production time. Robotic automation reduces labor dependency, addressing challenges related to skilled labor shortages in construction. This allows manufacturers to produce complex facade systems with fewer human resources while maintaining high standards of safety and quality. It also enables the integration of complex designs, such as curved or custom-shaped panels, which would be challenging and time-consuming with manual processes.
Another benefit of automated panel manufacturing is the overall thermal performance of the units. Tasks like cutting, assembling, and installing elements such as window frames, insulation, and cladding can now all be done with the precision of robotic systems. Design elements like thermal breaks and enhanced air sealing can be consistently and repeatably manufactured. For the builder, this can mean that all building envelope components can be code-compliant before they arrive on the jobsite.
“There are so many benefits for builders when it comes to panelization,” notes Ehret. “It saves on time, it saves on labor, it increases safety during installation.” After being built in a factory, the finished product can be taken apart, brought out to the building site, and put up successfully in days instead of months or even years in some cases. “With the integrated fenestration, modular companies can include all glass entrances, aluminum frame doors, slider windows, and really anything the architect can design,” Ehret says.
The shift towards prefabrication and modular construction has transformed the way architects approach building design. Prefabricated exterior panels simplify the process of achieving a high-performance building envelope by providing complete assemblies that include all necessary elements, from air barriers to exterior cladding. For architects, this means that design time can be spent focusing on architectural aesthetics and performance goals rather than managing the complexities of coordinating multiple trades on-site.
CONCLUSION
The low-rise multifamily housing market has evolved significantly in response to shifting occupant needs, technological advancements, and a growing emphasis on energy efficiency. Innovations in prefabrication and modular construction have further transformed the industry through the use of robotics and automation.
Buyers and renters in the multifamily market today are seeking homes that are comfortable, energy-efficient, larger, and that can provide greater access to daylight and the outdoors. These trends coincide nicely with the automation of panelized systems capable of prefabricating larger panelized systems that incorporate larger window openings while not diminishing building performance.
Of the ingredients necessary to create the best of both multifamily worlds – an energy-conscious and aesthetically comfortable home – aluminum remains a popular choice in the specification of windows and door framing. The natural attributes of aluminum work in harmony with energy efficiency goals, especially when proper thermal breaks are installed to support more sustainable buildings. At the same time, the thin frames of aluminum create the opportunity to invite more sunlight into the living space, helping address the full range of biophilic needs of the home’s residents, and the work-from-home community. Innovation, faster building, and the rise of automation have all worked in tandem to benefit these developments.
END NOTES
1https://www.nahb.org/Other/Consumer-Resources/Types-of-Home-Construction/Multifamily 2https://www.energy.ca.gov/sites/default/files/2022-08/CEC-400-2022-010_CMF.pdf
Andrew A. Hunt is Vice President of Confluence Communications and specializes in writing, design, and production of articles and presentations related to sustainable design in the built environment. In addition to in-structional design, writing, and project management, Andrew is an accomplished musician and voice over ac-tor, providing score and narration for both the entertainment and education arena. www.confluencec.com. www.linkedin.com/in/andrew-a-hunt-91b747/.