Specifying Sustainable Concrete
Influence of Prescriptive Specifications on Sustainability, Performance, and Cost
Common prescriptive requirements found in concrete specifications and their effects on performance, including sustainability and cost, are summarized in Table 1. Most of these requirements do not support sustainability goals and often increase the cost of concrete.
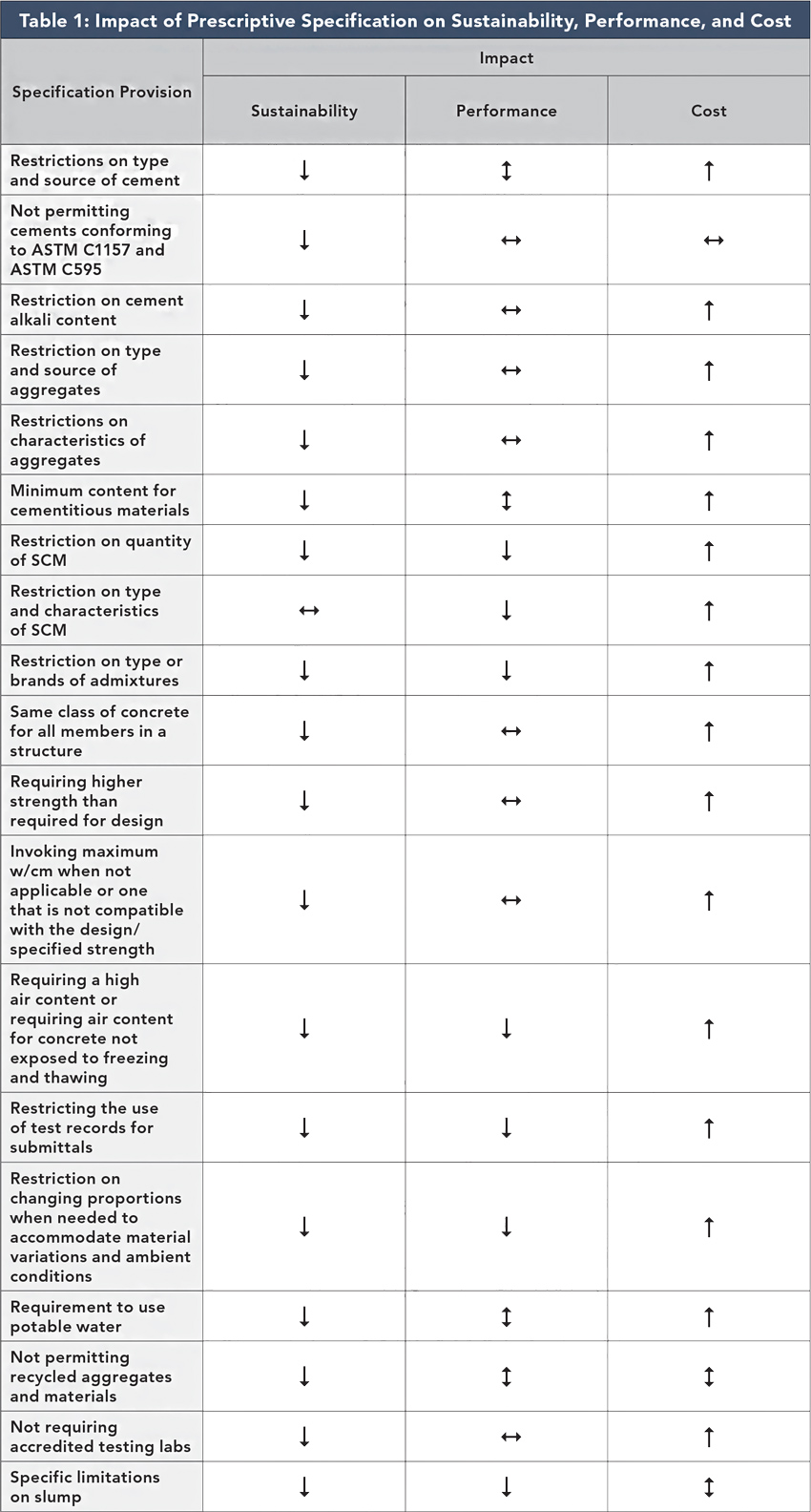
The intended concrete performance can be attained without specifying prescriptive requirements. The following is a detailed discussion of how the prescriptive criteria outlined in Table 1 can influence the performance and sustainability of concrete.
Cement type and source: Specifications often restrict the type (e.g., ASTM Type II) of cement or use of certain sources. Unless there is a building code requirement or specific reason for durability or other property, these restrictions should be avoided. These restrictions may force the use of materials that are unfamiliar to the producer, require a greater over-design, cause incompatibility with other materials, and require material to be transported a longer distance. The use of innovative products may be prevented. These restrictions do not support environmental goals and most often increase the cost of concrete.
Cement specification: Specifications often restrict the use of cements to ASTM C150. Blended cements conforming to ASTM C595 and performance cements conforming to ASTM C1157 are optimized for performance by cement manufacturers and often have a lower carbon footprint. These include portland-limestone cements (Type IL) and those blended with pozzolans (Type IP) and slag (Type IS). Permitting the use of blended cements supports sustainability. Cost implications are neutral. Concrete producers still have the flexibility of using additional SCMs to develop mixtures to meet the needs of a project.
Low-alkali cement: Specifications often require the use of a low-alkali cement to minimize the occurrence of deleterious expansive cracking due to alkali-silica reactions. Manufacturing low-alkali cements increases the use of natural resources and energy and can increase waste generation during cement manufacture. It should be noted that a recent revision to ASTM C150 has removed the option to order a low-alkali cement. It is recognized that the total alkali content in concrete from the cement is more significant. Mitigation of alkali-silica reactions can be accomplished using SCMs and admixtures. Requiring the use of low-alkali cement will increase cost and not support environmental goals. It should be noted that alkali-silica reactivity is only a concern when concrete is exposed to moisture; therefore most concrete in buildings is not affected.
Type and source of aggregate: Specifications may restrict the aggregate type and require the use of a specific source, such as crushed versus gravel, mineralogy, specific supplier or source, etc. This could ultimately force the use of materials that the producer may not be familiar with and prevent mixtures from being optimized for performance. The cost of aggregate might increase due to transportation. These requirements will not support sustainable development and can adversely impact performance. There may be situations where imported aggregates may be necessary. Examples of this include higher modulus or for architectural concrete.
Characteristics of aggregates: Specifications often place restrictions on the characteristics of aggregates, such as grading, specific gravity, particle shape and size, etc.. In some areas, local aggregate supplies may not comply with all requirements of referenced specifications, such as ASTM C33, but have a good history of use. This allowance is recognized in the building codes. However, when the requirements prevent the use of local materials or require use of materials that are not commonly used or locally available, it will increase cost and detract from sustainable development without significant benefits in concrete performance.
Limits on cement content: Many specifications impose minimum cement content for different classes of concrete. Requiring minimum cement content constrains the innovation of the concrete producer to optimize concrete mixtures and can result in inherent incompatibility with other requirements of the specifications, such as strength or w/cm. These can result in unintended consequences, such as increased volume changes due to temperature or drying shrinkage that will result in cracking or reduced durability. It is a fallacy to assume that higher cement content results in improved durability. Minimum cement content requirements can impact cost and environmental impacts with questionable benefits to quality, performance, and durability. On the other hand, attempts to force green construction should not set limits on maximum cement content. This could compromise constructability or performance of concrete in the structure resulting in reduced service life.
Quantity of SCM: Some specifications place limits on the quantity of SCMs. Often the use of more than one type of SCM is prohibited. This prevents optimizing concrete mixtures for performance and durability. The only building-code restriction is for exterior concrete subject to application of deicing chemicals. Maximum limits on the quantity of SCM increases cost and does not support sustainable development. Increasingly, projects seeking green certifications impose prescriptive requirements on concrete mixtures, such as minimum replacement for cement or minimum recycled content. These requirements can often impact the performance of fresh and hardened concrete properties, such as setting characteristics, ability to place and finish, and rate of development of in-place properties. In the long run, this may impact the quality of construction or the service life of the structure. The implication to initial cost may be reduced, but it could cost more in the long term. Alternatives to limiting quantities of SCM to lower environmental impact are discussed later in this course.
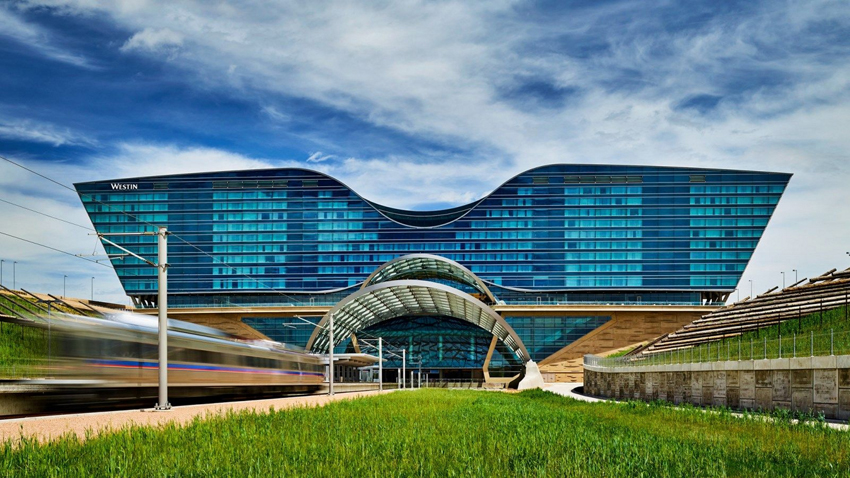
Figure 3: The Denver International Hotel & Transit Center used complex mix designs, including high-strength, self-consolidating, and lightweight concrete, for the transit and hotel canopy abutments, the hotel ballroom’s transfer beams and slab, and the structure’s sloping roof deck. Many of the walls and columns within the structure are “architecturally exposed,” requiring a clean and attractive finish. Beyond being able to fulfill the project’s design challenges, builders chose concrete for its fire resistance and strength.
Type and characteristics of SCMs: Specifications often prohibit the use of some types of SCMs or impose restrictions over and above those in the ASTM material specifications—such as lime content, alkali content, loss on ignition, or grade of slag cement. These will prevent the use of locally available materials that likely have good past performance and will require materials to be imported. The result will increase cost and detract from meeting environmental goals, while the impact on performance is questionable.
Type and brand of admixtures: Most specifications include a list of specific admixture brands and suppliers. Often the listed products are no longer available in the market. Concrete producers often have business relationships with admixture suppliers and experience with use of certain products. Forcing the use of specific products will impact the ability of the concrete producer to provide concrete mixtures of consistent quality and performance.
Same class of concrete for all components: Concrete members in a structure are often designed based on different strength levels and exposure classes. The requirements for foundations may differ from beams and columns; slabs may have different requirements. Specifications often indicate the same class for all of the concrete on a project. This can cause problems during placing and finishing. There are considerable cost savings and environmental benefits if the concrete is specified as required for the different structural members on a project. For example, it makes sense to use high-strength concrete for columns and shear walls, but it rarely benefits slabs and beams. Also, exposure classes should be assigned to specific components. For example, concrete that is protected from the environment and not subject to freezing and thawing should not have the same exposure class as concrete that is exposed to weather.
Higher strength than required by design: If a higher strength is specified or required for durability, the designer should use this to his or her advantage when designing the structure and minimize the section size when applicable.
Max w/cm when not required: The building code requires the use of a maximum w/cm for durability and assigns a minimum specified strength that is in alignment with the required w/cm. Many specifications incorporate limits on w/cm for elements not subject to durability concerns. This includes all interior concrete. Imposing a low w/cm limit likely increases the cement content of concrete mixtures and affects the ability to place and finish concrete. The use of a max w/cm, where not required, increases cost and does not support sustainable development.
Air content: Air-content requirements for concrete vary by aggregate size because the volume of paste changes. It is further permitted to reduce the specified air content when the specified strength exceeds 5,000 psi. In many vertical members that will not be critically saturated and require a high design strength, air-entrained concrete may not be required. Air-entrained concrete is not required for interior structural members. Many regions in the southern United States have a long history of durable concrete that is not air entrained, even though temperatures may occasionally dip below freezing. Most specifications state a constant air-content requirement regardless of aggregate size and often increase it, assuming this will improve freeze-thaw durability. Air content reduces strength, and additional cement is required to offset this strength decrease. This can result in increased propensity for thermal and shrinkage cracking. Specifying air content that is not appropriate for a structural member increases cost and materials, while likely reducing performance and sustainability.
Use of test records for submittals: Specifications often indicate that the concrete mixture should be designed to produce an average strength at a fixed value greater than the specified strength. This essentially prohibits the use of past test records that allow for a statistically based average strength. This discourages concrete producers that have good quality control from optimizing concrete mixtures to a lower strength level and thereby conserving materials. This requirement increases cost, does not support sustainable concrete, and could result in unintended problems due to high cementitious materials content.
Restriction on changes to mixtures: Ingredient materials vary, as do environmental conditions during the project. Real-time adjustments are necessary to accommodate these variations and ensure consistent concrete characteristics. Several specifications prohibit such minor changes to concrete unless a submittal, often with supporting test data, is provided to the engineer of record. It is recognized that the engineer of record should be notified for major revisions to mixtures, but prohibition of changes can cause considerable negative impact to concrete performance.
Use of potable water: ASTM C1602 addresses the quality of water that can be used to produce concrete, and it includes provisions to permit the use of non-potable water with proper testing and evaluation. Specifications that prohibit the use of non-potable water increase cost and result in the generation of considerable volumes of waste water. Specifications that require the use of potable water detract from sound environmental management practices at concrete production facilities.
Recycled materials and aggregates: There are applications for concrete that can accommodate the use of recycled aggregates or other materials with minimal impact to concrete quality. Crushed returned concrete can be used as a portion of the aggregate in concrete for some applications to conserve virgin materials and minimize waste. The use of recycled material can contribute to credits in green construction rating systems. The use of crushed concrete as aggregate is recognized in industry standards. Judicious use of these materials will reduce cost and conserve natural resources and landfill space with minimal impact on performance.
Reliable testing: While this may not seem pertinent, improper testing procedures will increase variability and result in greater over-design of concrete mixtures. When concrete producers are aware of improper testing, they protect themselves by increasing the cementitious materials in concrete mixtures. This results in increased cost and does not support sustainable development. Selection of testing agencies should be based on quality of work, conformance to ASTM C1077, and having certified personnel conducting tests. Test reports should be distributed to producers as soon as they are available to help identify potential problems early.
Specific limitations on slump: Slump should be selected by the contractor and concrete supplier based on the placement and finishing requirements of the concrete. With the use of water-reducing admixtures, slump cannot be taken as a representation of the quantity of water in the mixture. The target slump can be provided to the engineer of record in the submittal and be used as a basis for quality assurance. Placing limits on slump usually results in reduced sustainability and performance and can increase cost.