Design Considerations for Commercial Fenestration Systems
Curtain-Wall Systems
Curtain wall systems are non-load-bearing exterior walls that hang from the building’s structure like a curtain beyond the face of floor slabs, regardless of construction or cladding material. These systems can span multiple stories and are designed to withstand environmental forces such as wind and seismic activity. Usually, a curtain wall describes aluminum-framed systems supporting glass, panels, or louvers. However, steel, fiberglass, wood, composite, stone, and other products may also be incorporated into the system. This flexibility in material options makes curtain walls a highly attractive option for architects hoping to include unique or creative features in the design.
When properly designed, specified, and installed, curtain walls provide superior performance in terms of air and water infiltration, thermal insulation, and structural integrity. They are designed to accommodate building movements and resist environmental forces, ensuring long-term durability. The use of advanced glazing technologies and materials enhances the energy efficiency of curtain walls, making them suitable for high-performance buildings. However, these benefits come at a higher cost compared to storefront and window wall systems.
History of Curtain-Wall Glazing Systems
The concept of curtain walls can be traced back to the late 19th century during the Industrial Revolution. Early curtain walls were primarily constructed using cast iron and large glass panes. The Crystal Palace, designed by Joseph Paxton for the Great Exhibition of 1851 in London, is often cited as an early example of a curtain wall structure. It featured a cast-iron framework with large glass panels, showcasing the potential of using glass and metal in building exteriors.
Over time, cast iron was replaced by aluminum with its lightweight and corrosion-resistant qualities. Glazing technologies like insulating glass units (IGUs), double-glazed and triple-glazed units, along with low-emissivity (low-e) coatings helped enhance the energy efficiency and thermal performance of curtain walls. Today because of the performance attributes and aesthetic appeal, curtain walls are a popular choice for multistory buildings, especially high-rise urban construction.
Performance Advantages of Curtain-Wall Systems
Of the three glazing systems, curtain-wall systems offer the greatest opportunity for designing a high-performance building. While stick and window wall systems can satisfy code requirements and be enhanced to achieve greater thermal, acoustic, and structural performance, curtain-wall systems may be pre-loaded with these attributes.
Curtain walls are designed to span multiple floors and are anchored to the building’s structural frame. This design allows them to distribute wind loads and other environmental forces more effectively across the building structure. The strength of the anchorage also allows curtain wall systems to withstand seismic activity.
The anchorage schema helps reduce deflection from wind pressure, protecting vulnerable seals at joints and connections from excessive wear and tear. Overall, curtain walls have fewer points of access for water migration than stick-built and window wall systems. As noted earlier, the fewer joints and penetrations in the building envelope, the less the risk of water migration through faulty seams.
Installation Methods of Curtain-Wall Systems
Curtain wall installation is more complex than window wall systems but utilizes many of the same principles. Installation typically involves prefabricated units that are assembled on-site. As with window walls, curtain walls can be installed using stick systems or unitized systems. A third option, the hybrid system is also available. While unitized curtain-wall systems, also known as “cassettes” are factory built with glazing pre-installed, stick systems and sometimes hybrid curtain-wall systems require glazing installation on the jobsite.
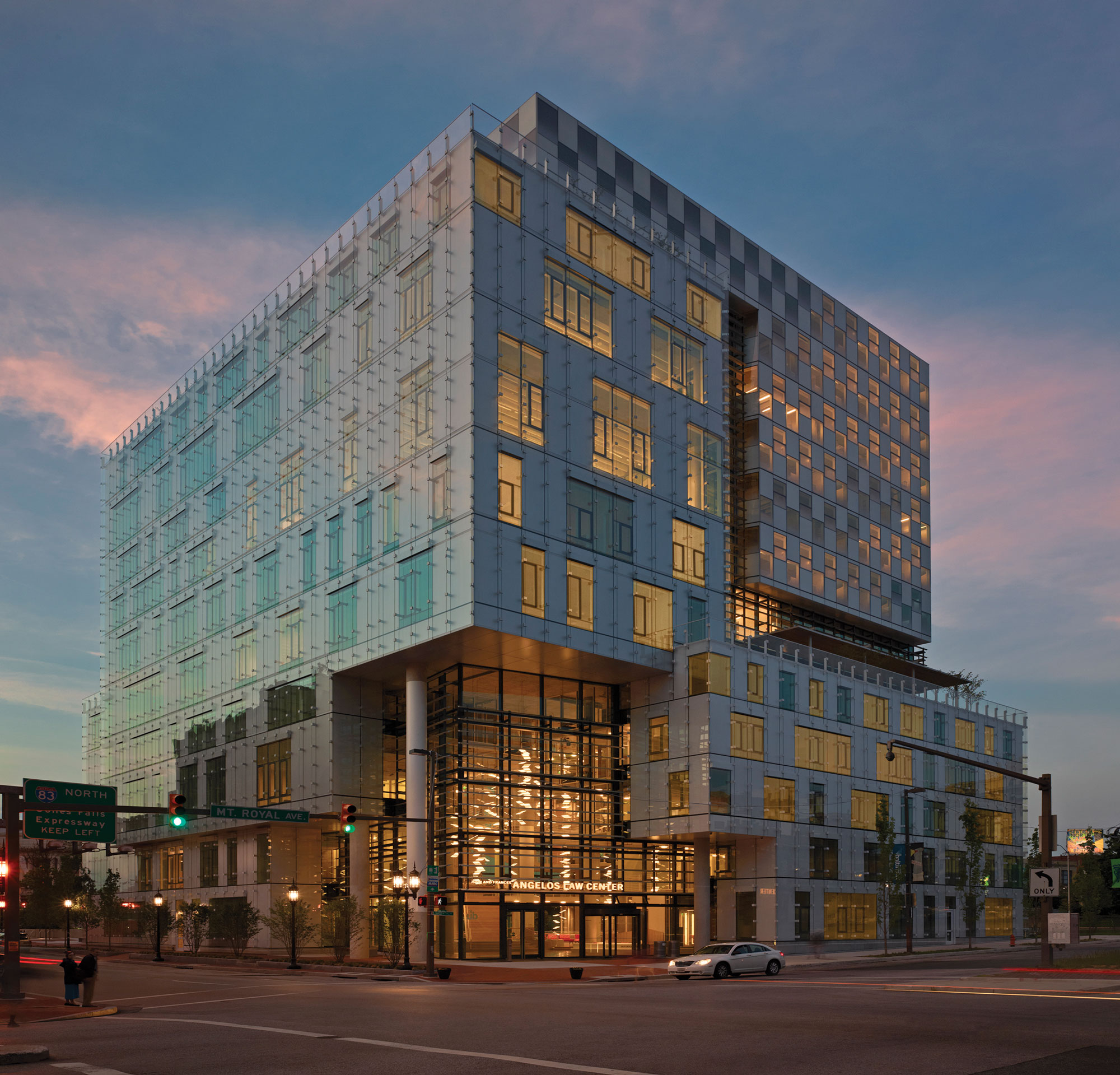
Photo: Wheaton & Sprague Engineering; courtesy of NGA
Curtain wall systems are designed to offer large, clear views, thereby enhancing visibility, letting ample natural light into the building, and providing inviting views of the street.
Hybrid Curtain-Wall Installation
The hybrid system combines the benefits and basic installation elements of both the stick and unitized systems. It allows for some prefabrication while retaining flexibility for on-site adjustments. This method can be tailored to specific project needs, balancing cost, time, and performance considerations. Hybrid systems are very flexible and may or may not include the factory installation of infill and glazing materials.
Key components of the curtain wall, such as vertical mullions, horizontal transoms, and sometimes glazing units, are partially assembled in a controlled factory environment. This ensures high precision and quality control. The pre-assembled units or components are transported to the construction site and are typically smaller than fully unitized panels, making logistics and handling easier. On-site, the partially pre-assembled units are installed onto the building structure. The vertical mullions are first attached to the building’s structural frame, followed by the horizontal transoms.
If infill and glazing are not installed in the factory, glazing and other infill materials (like spandrel panels) are installed into the framework. This step may include sealing and weatherproofing to ensure the system’s integrity against air and water infiltration. In simple terms, the hybrid system creates a factory-built framework of exacting performance standards that is transported to the jobsite and secured to the structural components of the building. Once the frames are installed, glazing is installed. The connections and joints within the framework are already sealed, reducing the risk of water and air migration. Options on which type of fenestration system, styles, and installation methods can be challenging for architects and designers, which is why it is critical to keep pace with all the most recent developments and innovations.
Otto Ward, Architectural Design Manager and Business Development Manager for Garibaldi Glass understands the complexity of the current glass market. “Selecting between storefront, window wall, and curtain-wall fenestration systems has evolved from a relatively straightforward selection to a considerably more complex decision-making process, particularly with the introduction of more rigorous thermal and airtightness standards,” notes Ward. “To make an informed choice, it is essential not only to understand which systems are suitable for specific applications but also to assess their performance requirements. Utilizing thermal modeling will play a critical role in guiding the selection process and ensuring the chosen system meets the project’s specifications.”
Methods of Glazing Curtain-Wall Systems
There are four basic options available for installation of glazing in curtain-wall systems using stick or hybrid curtain-wall systems: captured glazing, structurally glazed, toggle-glazed, and point-supported. Each option offers advantages and drawbacks that range from structural integrity to aesthetic appeal.
Captured Glazing: Captured glazing involves securing the glass panels within a frame using mechanical fasteners, pressure plates, and gaskets to weatherproof and seal the unit. This method provides strong structural support and is widely used for its reliability and ease of installation.
After the grid framework has been installed─either via stick or hybrid system─glass panels are lifted and positioned into the frame and rest against interior gaskets within the mullions and transoms. The positioning of the glass is critical to ensure it aligns properly and maintains the intended design.
Once in position, pressure plates are placed on the exterior side of the mullions and transoms, over the edges of the glass panels. These plates are fastened with screws, applying uniform pressure to hold the glass firmly in place. Gaskets are installed around the glass edges to create a weather-tight seal, and additional sealant may be applied to enhance waterproofing and prevent air infiltration. This method offers strong structural support and reliable sealing, making it suitable for high-performance curtain wall applications.
Structurally Glazed: In structurally glazed systems, the glass panels are bonded to the frame using high-strength structural silicone sealants, eliminating the need for pressure plates and creating a smooth, uninterrupted glass surface. This method allows for larger glass panels but requires precise fabrication and installation to ensure structural integrity and performance.
Vertical mullions and horizontal transoms are installed to form the structural framework of the curtain wall. This can be either stick-built or a hybrid system. Glass panels are placed against the interior side of the frame allowing for installation within the building and reducing the need for scaffolding and cranes. The structural silicone sealant is applied to bond the glass to the mullions and transoms and provides the necessary structural support and weatherproofing. Additional sealant is applied to ensure airtight and watertight seals around the glass edges, and spacer blocks are used to maintain consistent joint widths and ensure proper adhesion.
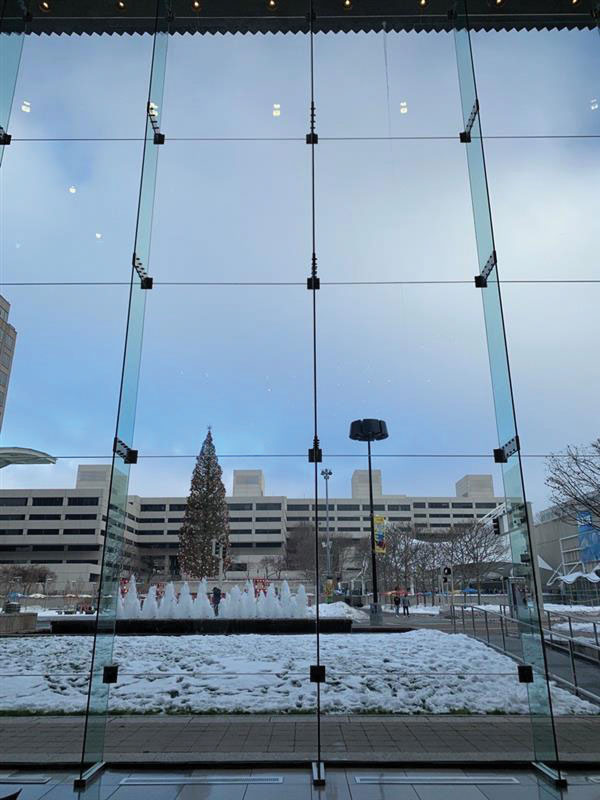
Photo courtesy of NGA
Because of the rapidly changing technologies available for storefront, curtain wall, and window wall systems, architects are well advised to keep current on recent trends.
Toggle-Glazed: Toggle-glazed systems use a toggle mechanism to secure the glass panels to the frame. This method combines the benefits of captured and structurally glazed systems, providing a clean appearance with strong structural support. Toggle-glazed systems are gaining popularity for their ease of installation and maintenance.
Vertical mullions and horizontal transoms are installed, featuring grooves or channels to accommodate the toggle mechanism. The framework, usually a hybrid system, is designed to receive glass panels with minimal visible hardware.
Glass panels, often pre-fabricated with a toggle gasket or insert, are placed against the frame. Toggles, which are mechanical clips, are inserted into the frame’s grooves, securing the glass from the inside. Once the glass and clips are in place, the toggles lock the glass panels in place, ensuring they are firmly attached to the frame. Additional seals and gaskets may be applied to enhance weatherproofing.
The toggle-glazed style of installation can provide enhanced protection for the building against water and air intrusion because it incorporates both mechanical- and captured-glazed style adhesives. Another benefit of the toggle system is that if an individual glass panel needs to be replaced, it can be removed and reinstalled without disrupting adjacent panels. This provides easier maintenance for the building owner over the life of the building and is especially helpful in areas of extreme wind and weather events, where glazing may be damaged by airborne projectiles.
Point-Supported: Point-supported systems use a series of metal fittings (spiders) to hold the glass panels in place at specific points. This method allows for maximum transparency and minimal visual obstruction, making it ideal for applications where aesthetics are a primary concern. Point-supported systems require precise engineering to ensure load distribution and structural stability.
A primary structural framework often made of steel or aluminum is installed to support the point fixings. Spider fittings or other point-support mechanisms are attached to the structure at pre-determined points.
Glass panels are fabricated with pre-drilled holes at specific locations to accommodate the point supports. The glass is lifted and positioned so that the holes align with the point supports. Once in position, bolts or other hardware used to attach the glass panels to the point supports. Gaskets or other sealing materials are used to ensure a weather-tight connection around the points.
The point-supported glazing system allows for large, uninterrupted surfaces that can offer striking design aesthetics. The minimal interruption provides maximum daylighting for the building interior, which can help with biophilic design goals and reduce energy use of artificial lighting.
Some of the drawbacks to point-supported systems include cost. This style of installation can be more cost-prohibitive than captured or toggle glazed systems. Also, correct alignment and drilling of the glass panels is critical for a successful installation with little margin of error. To this point, the holes in the glass need to be considered basic penetrations in the building envelope, so sealing around each point-support is critical.
Conclusion
Given the wide range of commercial fenestration options available, projects are best served by architects and designers who understand the types, limitations, and basic installation processes for storefront, window wall, and curtain-wall glazing systems.
Storefront systems offer an economical and visually appealing solution for ground-level applications, providing clear views and easy access, albeit with moderate performance in thermal and acoustic insulation. On the other hand, window wall systems bridge the gap between cost and performance, making them suitable for mid-rise to high-rise applications where enhanced thermal and acoustic properties are desired. Finally, curtain-wall systems stand out for their superior performance and versatility, capable of withstanding environmental forces while delivering a sleek, modern facade.
Understanding these distinctions helps architects and builders select the appropriate system to meet specific project requirements, ensuring that buildings are not only visually compelling but also energy-efficient, resilient, and comfortable for occupants.
Andrew A.Hunt is Vice President of Confluence Communications and specializes in writing, design, and production of articles and presentations related to sustainable design in the built environment. In addition to instructional design, writing, and project management, Andrew is an accomplished musician and voice-over actor, providing score and narration for both the entertainment and education arena. www.confluencec.com, www.linkedin.com