Weathering the Unstable Market
Bringing the Value of Resilience to the Table
“In the ever-changing industry of home building, it is important to continually assess building needs and market trends. Resiliency issues, for example, have become increasingly prevalent in the building industry over the last decade,” said James W. Tobin, III, President and Chief Executive Officer, NAHB. “Changes to regulations, codes, and consumer demands to ensure homes are prepared to better withstand storms, droughts, and other natural disasters have created both uncertainty and opportunity for builders and home buyers.”13
Today’s homes are called to go beyond lessening their environmental impact; they also need to actively mitigate the effects of the environment. The most common natural hazards can be broken into five categories: wind, flood, fire, earthquake, and temperature. Any home may face damage from environmental hazards, prompting builders to implement resiliency practices to reduce such risks. Three-quarters of builders surveyed by the NAHB say they mitigate for at least one of these five hazards.14
Just as builders are actively embracing resilience, homeowners are growing increasingly aware of its value. In a survey conducted on behalf of the American Property Casualty Insurance Association (APCIA), 85% of homeowners supported the adoption of the latest building codes by their communities to ensure new construction meets stringent disaster-resilient standards. Seventy-five percent of homeowners were willing to upgrade certain home materials to meet building code standards, enhancing their properties' resilience. And a majority, 80%, of homeowners supported efforts to restrict development in storm/wildfire-prone areas to curb rebuilding and repair costs.15
Specifying Outdoor Features with Assurance
Patios, decks, pergolas, and gazebos are features highly valued by a prospective buyer and homeowner. Specifications allow the design team and builder to protect that investment from the elements with assurance.
The American Wood Protection Association (AWPA) is a non-profit organization that promulgates voluntary wood preservation standards. AWPA Standards are developed by its technical committees in an ANSI-accredited consensus-based process that involves individuals from all facets of wood preservation: producers of preservatives and preservative components; producers of treated and untreated wood products; end users of treated wood; engineers, architects, and building code officials; government entities, academia, and other groups with a general interest in wood preservation. AWPA's Standards are universally specified for wood preservation in the USA and are recognized worldwide.16
Professionals required to develop and maintain project specifications depend on AWPA Standards and its Technical Committees' expertise in the field of wood protection. Products specified in AWPA have been researched, evaluated through an ANSI-accredited process, and peer-reviewed by the largest body of wood preservation and protection experts in North America. Specifiers face a rapidly increasing diversity of preservatives and species in the marketplace, making it important to specify products that meet AWPA Standards.17
Once materials are delivered to the jobsite, the design team and builder can easily verify that they comply with AWPA Standards. Products that are compliant with AWPA standards feature a legible tag that states their status as an AWPA-standardized product. To determine conformance with AWPA Standards, the end tag will contain the following elements:
- AWPA Use Category: Examples are UC2, UC3B, or UC4A which describe the proper application for the treated wood product. The formal descriptions of the AWPA Use Categories can be found at https://awpa.com/images/standards/U1excerpt.pdf.
- Preservative Name and/or Code: Examples are Copper Azole (CA-C), Inorganic Boron (SBX), Micronized Copper Azole (MCA), among many others.
- Preservative Retention: The nominal amount of preservative retained in the wood as specified in Standard U1, such as 0.060, 0.15, or 0.31, which varies by the type of preservative used.
- Inspection Agency Logo: If the treating plant subscribes to third-party quality control, the logo of the accredited agency is displayed, along with a "check-mark" logo to make it easier to locate the agency information.
- >Manufacturer and Location: This information facilitates additional communication, in case a consumer information sheet or additional information on the product itself is required.
Selecting Pressure-Treated Lumber
Selecting the right pressure-treated lumber product for the project is also critical. Use Category Designations can help clarify decision-making.
End tags for lumber that meets AWPA standards will display one of these Use Category Designations.
- UC3B: Above ground
- UC4A: General above-ground/ground contact and freshwater use
- UC4B: Ground Contact/structural use, for critical structural, ground contact, fresh water, and saltwater splash
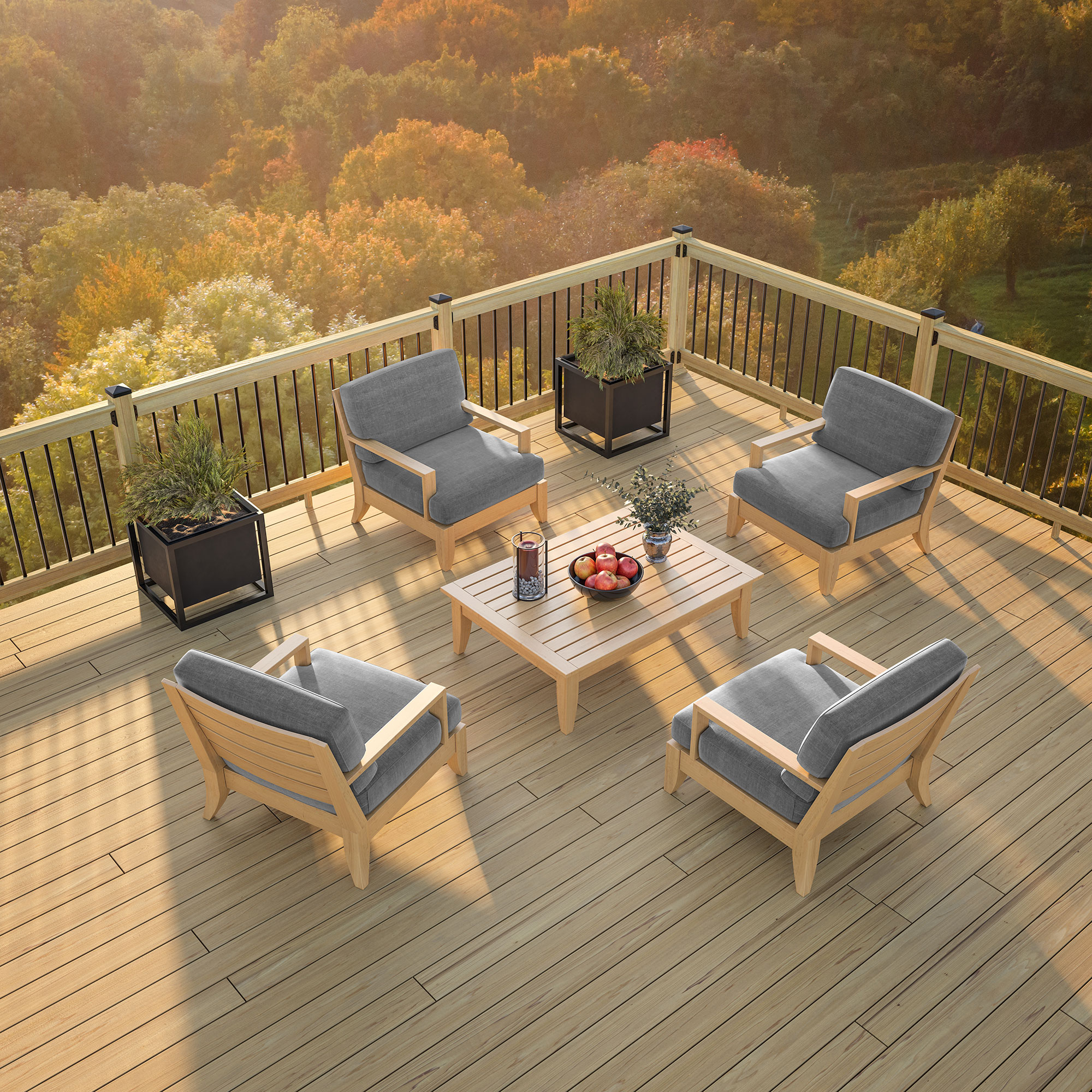
Photo courtesy ProWood
Advances in pressure-treated lumber products mean preservatives are EPA-registered and safe for handling and use. Color-treated lumber is guaranteed to resist fading, reducing future maintenance.
Light duty covers wood treated to an internal company standard. It is not meant for structural uses, and should not be used for applications that are critical to the integrity of a structure. Light Duty products also do not conform to the AWPA/ESR standards. These products are easily replaced and maintained and are generally backed by a 1-year warranty, though some products may carry a warranty of 10 to 20 years. Lumber with a Light Duty designation can be used above-ground and in some ground contact settings. These products can comprise West Virginia split rail fencing, any RP/DF/non-KD SYP fencing products/components, and any specialties, such as spindles or lattice, and round posts. For long-term structures that are difficult to replace, it's recommended to use ground contact products. It is best to use above-ground products (UC3B) only for areas that will not devolve to ground contact over time. For decorative landscape projects that are easier to replace, the use of light-duty products is acceptable.
Wood treated to (UC4A) ground contact standards is ideal for general-use situations where the wood may contact moisture, the ground, or be installed in a manner that subjects the wood to comparable ground contact conditions. These conditions may include factors like poor ventilation, tropical climates, or frequent exposure to moisture.
Examples of UC4A-approved applications include:
- Deck joists
- Beams
- Ledger boards
- Posts
- Stair stringers
- Certain deck board installations
Ground contact lumber applications must adhere to UC4A requirements when wood is used in the following scenarios:
- The application is difficult to maintain, repair, or replace (such as deck joists and ledger boards) and is critical to the performance and safety of the entire system/construction.
- The application is installed less than 6 inches from the ground.
- The application is at risk for poor air circulation (little airflow).
- The application is likely to have prolonged contact with vegetation or damp leaves.
- The application is exposed to frequent moisture.
- The application is used in a tropical climate.
If a project requires above-ground products, it is important to think through natural conditions. Areas where debris can accumulate over months or years can simulate ground contact conditions. Factoring this into the design of the project and selection of material on the front end can pay dividends over the life of the project.