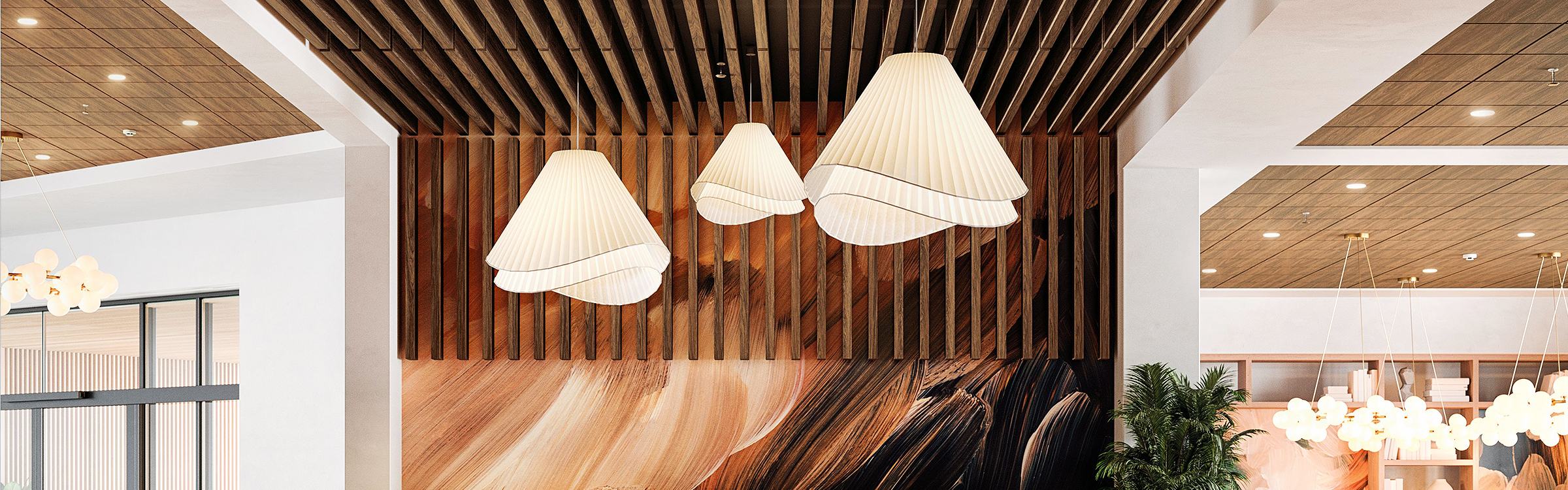
Sonic Shangri-la – The Art of Sound
Exploring the Harmony of Innovation, Design, and Acoustic Excellence
Sponsored by Armstrong World Industries
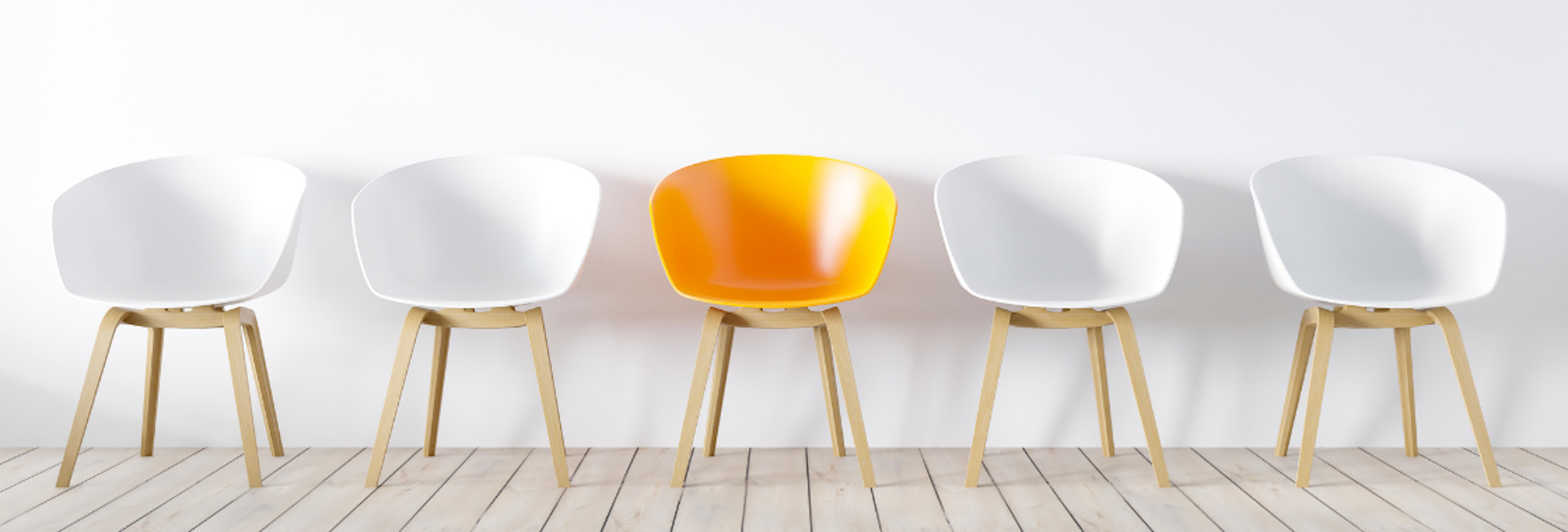
Next-Gen Leadership
Essential Training for Architecture Firm Growth
Sponsored by BQE Software
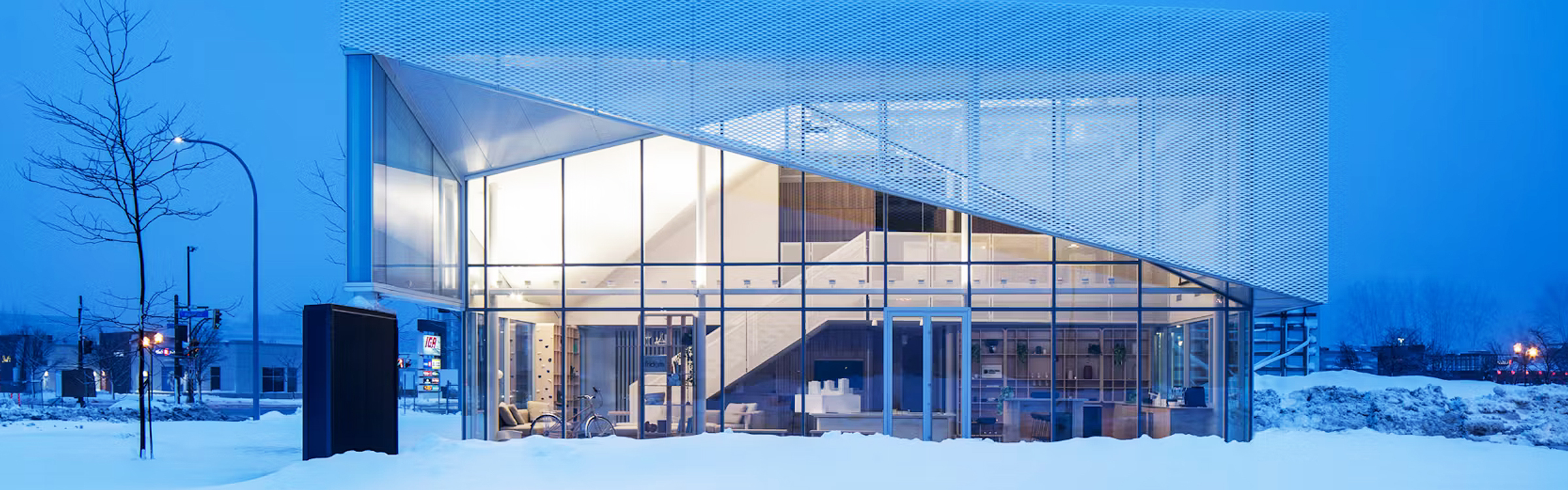
Expanded Metal and Perforated Mesh Interior and Exterior Applications
Starting a Design and Understanding Material Features & Benefits
Sponsored by AMICO Architectural Metal Systems
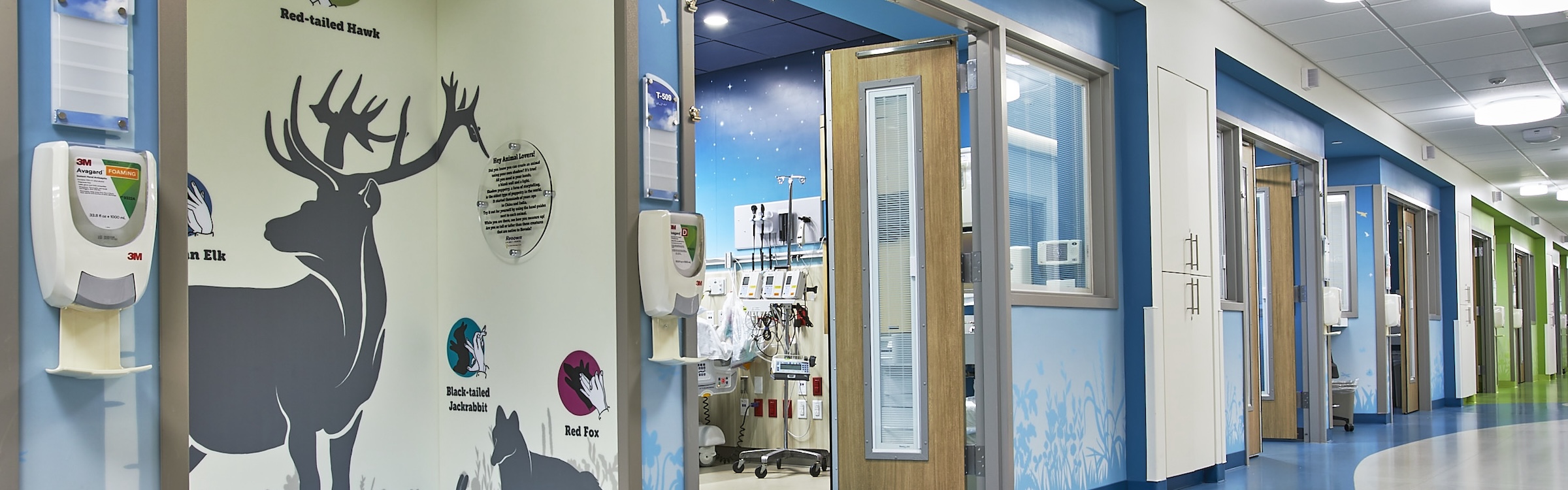
Built to Protect
Durable Wall Protection for Durable Buildings
Sponsored by Inpro